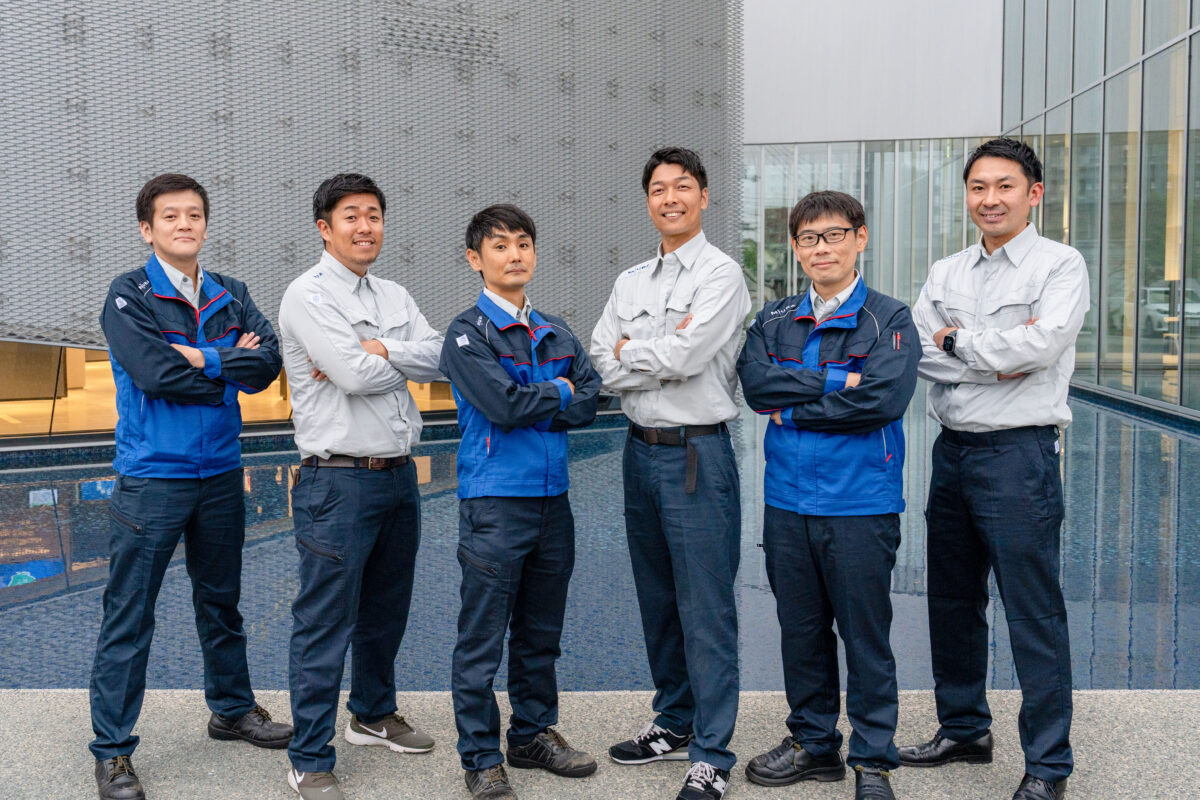
フィールドエンジニア×設計者 本音トーク!座談会
お題は、『設計者の思い ×FEの思い』。
密接な繋がりがありながらも、なかなか直接意見交換をする機会がないFEと設計者。
第3回目は、いよいよFEと設計者がご対面。
お互いの気持ちを共有することで、どんな化学反応が起こるのでしょうか!?
島根・鳥取のスタッフが考える、次のミウラplusの企画は?! 【ミウラplus 出張編集部会議@山陰 part3】
今回の企画 MENU
①わかって欲しい!メンテナンスの苦労と努力
~フィールドエンジニアたちの本音編~
②設計者のキモチ
〜安全性・品質・コストetc…葛藤しながらやっています〜
③フィールドエンジニア×設計者 本音トーク!座談会
参加者プロフィール
もりた だいき
森田大貴
MORITA Daiki
八王子中央メンテ 主任
プロフィール
2015年入社。趣味はゴルフ。料理好きで、お酒のアテを作って晩酌することも。得意料理はアヒージョ。今の悩みは、異動がないこと⁉
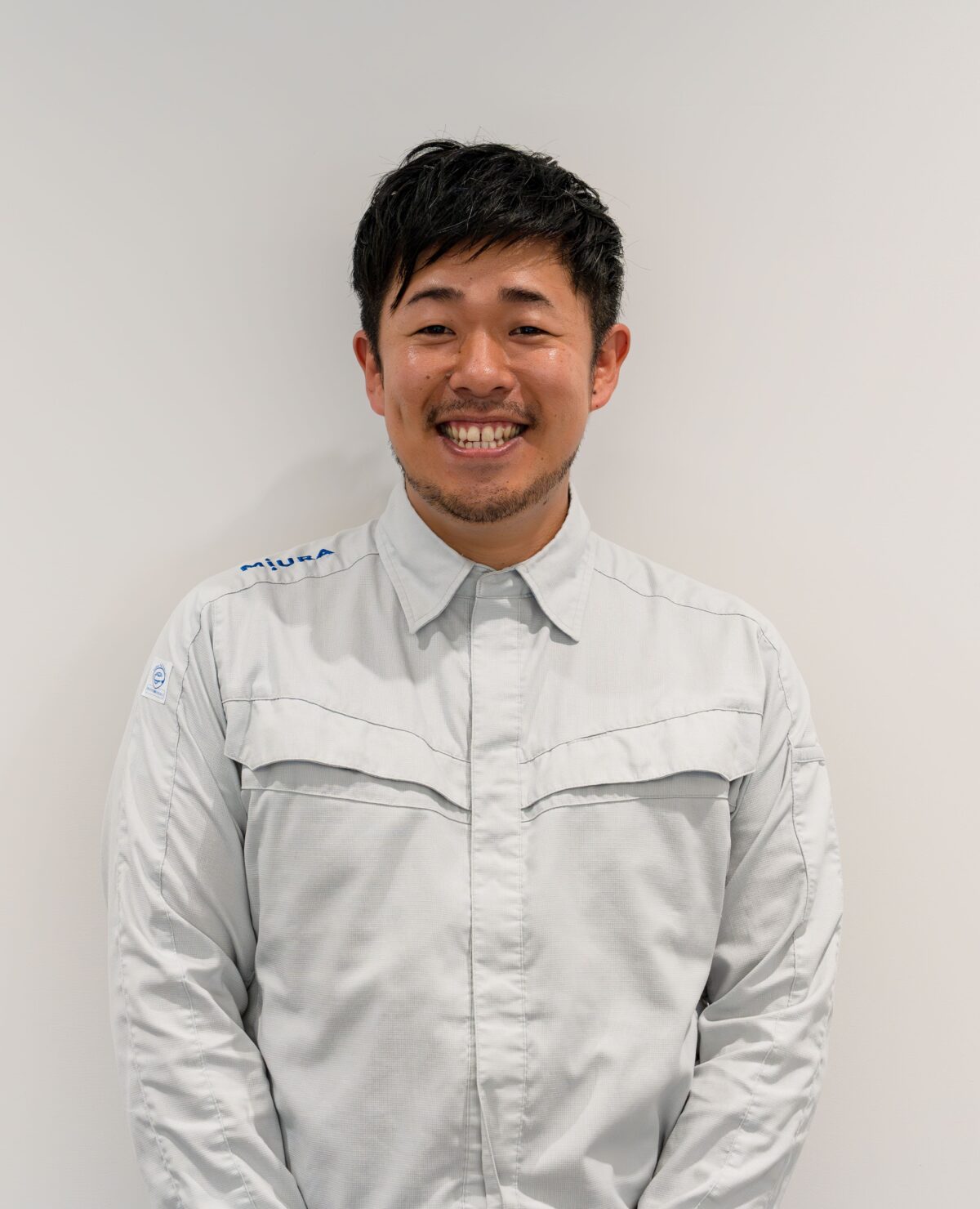
しらかた たかと
白方誉人
SHIRAKATA Takato
広島北メンテ 主任
プロフィール
2009年、製造グループ会社の三浦マニファクチャリング入社。自らの希望で、2018年に三浦工業に移籍。趣味はスポーツ観戦。公的資格取得にチャレンジ中…!
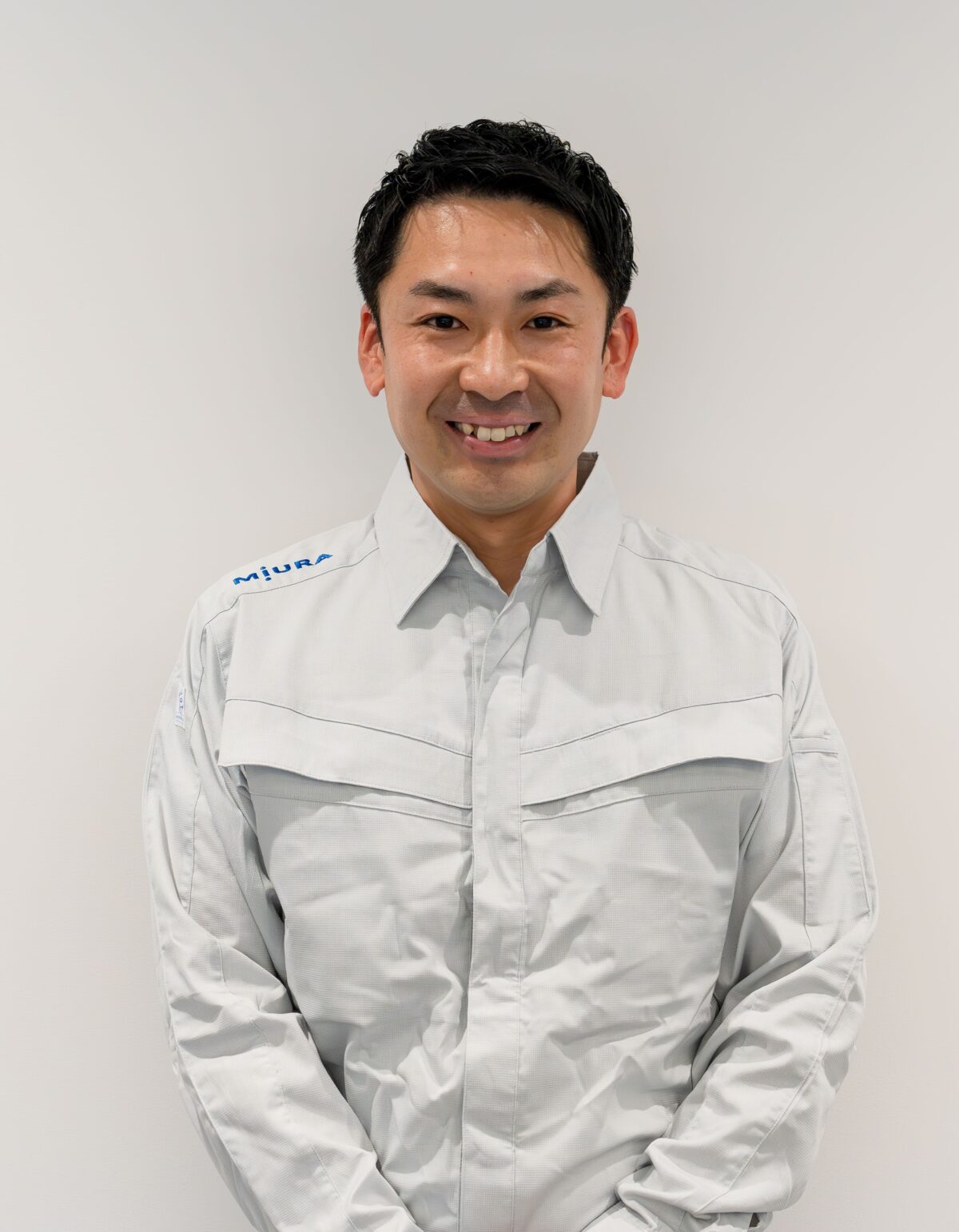
よしおか りょうた
吉岡凌汰
YOSHIOKA Ryota
三河中央メンテ 主任
プロフィール
2016年入社。三河西メンテ→三河中央メンテへ。趣味はゴルフ。ジビエが好き。海外勤務を志望しており、社内の「グローバル人材認定プログラム」を受講中。
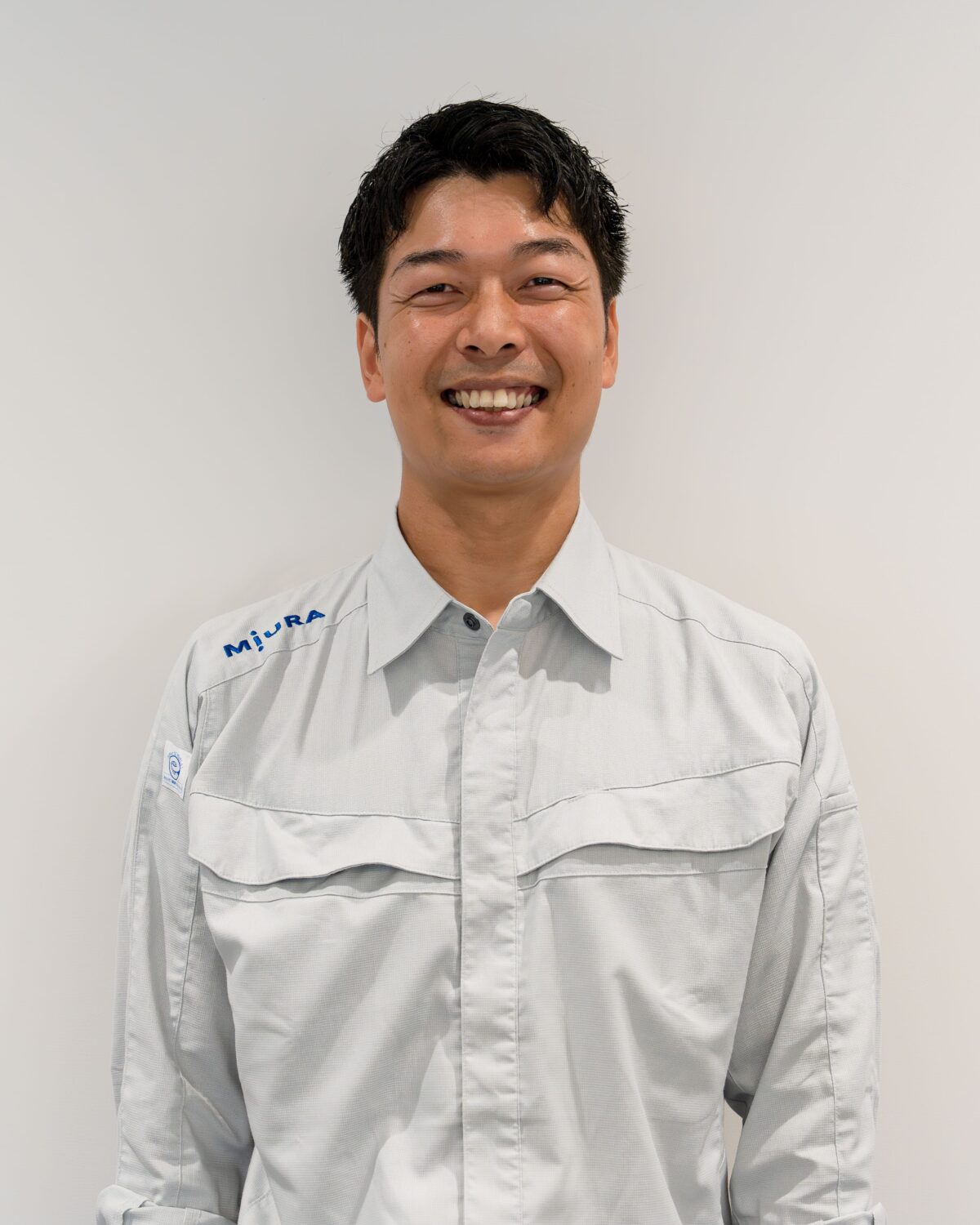
かみや よしてる
神谷 佳輝
KAMIYA Yoshiteru
ものづくり技術部 ものづくり技術課 係長
プロフィール
2006年入社。技術部量産設計課、アメリカ駐在部(5年間)を経て、ものづくり技術課へ。国内ボイラの量産維持対応を行っている。特技は数字を覚えること。
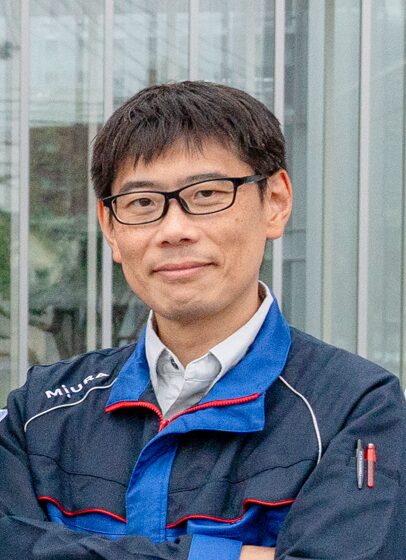
やまうち こうた
山内 孝太
YAMAUCHI Kota
ボイラ技術部 ボイラ技術課 主任
プロフィール
2007年入社。流体センサ技術部、熱機器特需部、グローバル技術部、熊谷支店(6年間)を経て、ボイラ技術部へ。標準ボイラの量産維持・品質向上を行う。単身赴任のため、家族とのTV電話が楽しみ。
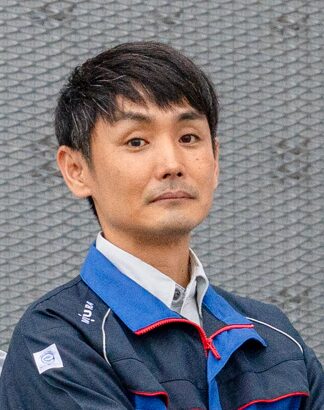
よしたけ じゅん
吉武 淳
YOSHITAKE Jun
ボイラ電機技術部 ボイラ電機技術課 主任
プロフィール
2015年入社。電機技術部、グローバル技術部を経て、ボイラ電機技術部へ。国内ボイラの電機設計、海外ボイラの電機設計支援を行う。趣味はスポーツ鑑賞(特に相撲)。
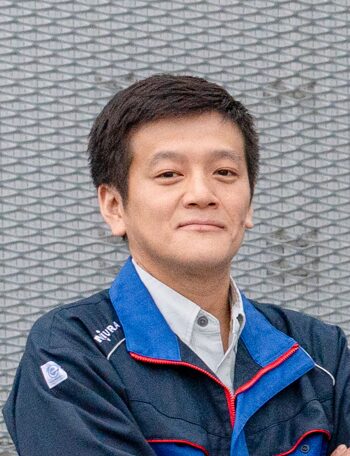
省スペースにこだわる理由
編集部:早速ですが、設計者の方々に質問です。ボイラがコンパクトになっているがゆえに、「メンテナンス作業がスムーズに行えない」という声もあるのですが、省スペースにこだわる理由や重要さを教えてください。
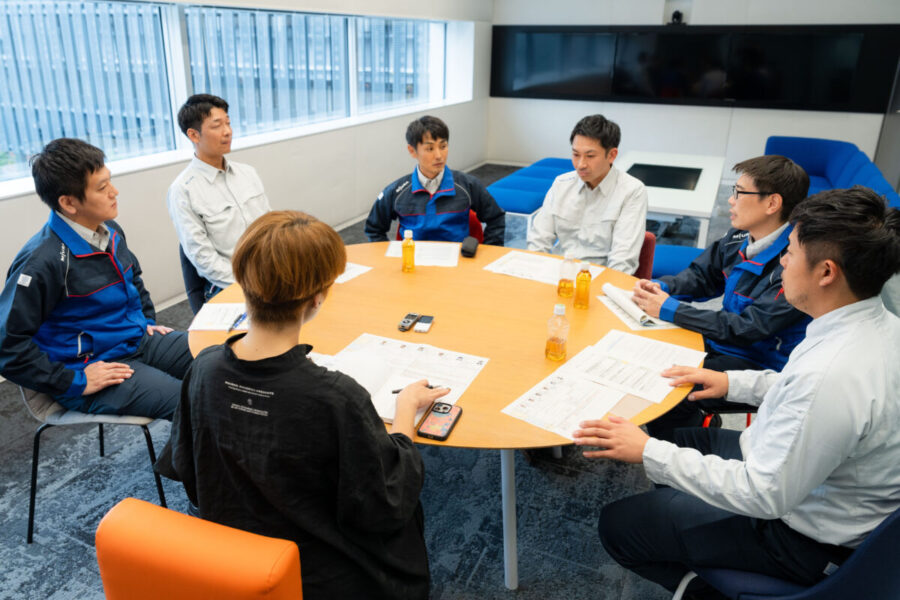
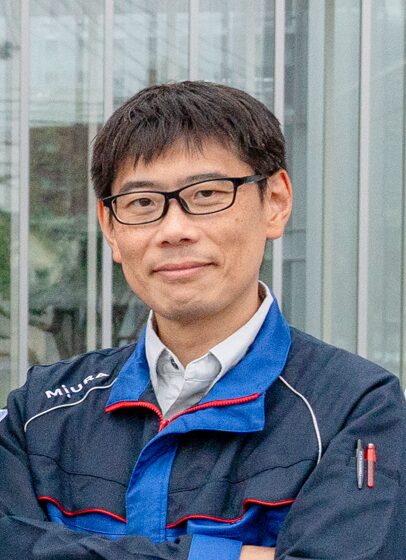
まずは、「お客様に買っていただくこと」が第一前提ですよね。海外に比べて、日本ではより省スペースの製品を求められることが多いです。特に製品幅に関しては、シビアにジャッジされていて「競合他社と比較して劣らないように」と営業担当者からも言われています。
そのような背景もあって、私がレイアウト設計を担当した「小型貫流蒸気ボイラSQ-3000AS」も、スペックを突き詰めて、幅1110mmとコンパクトに収めました。
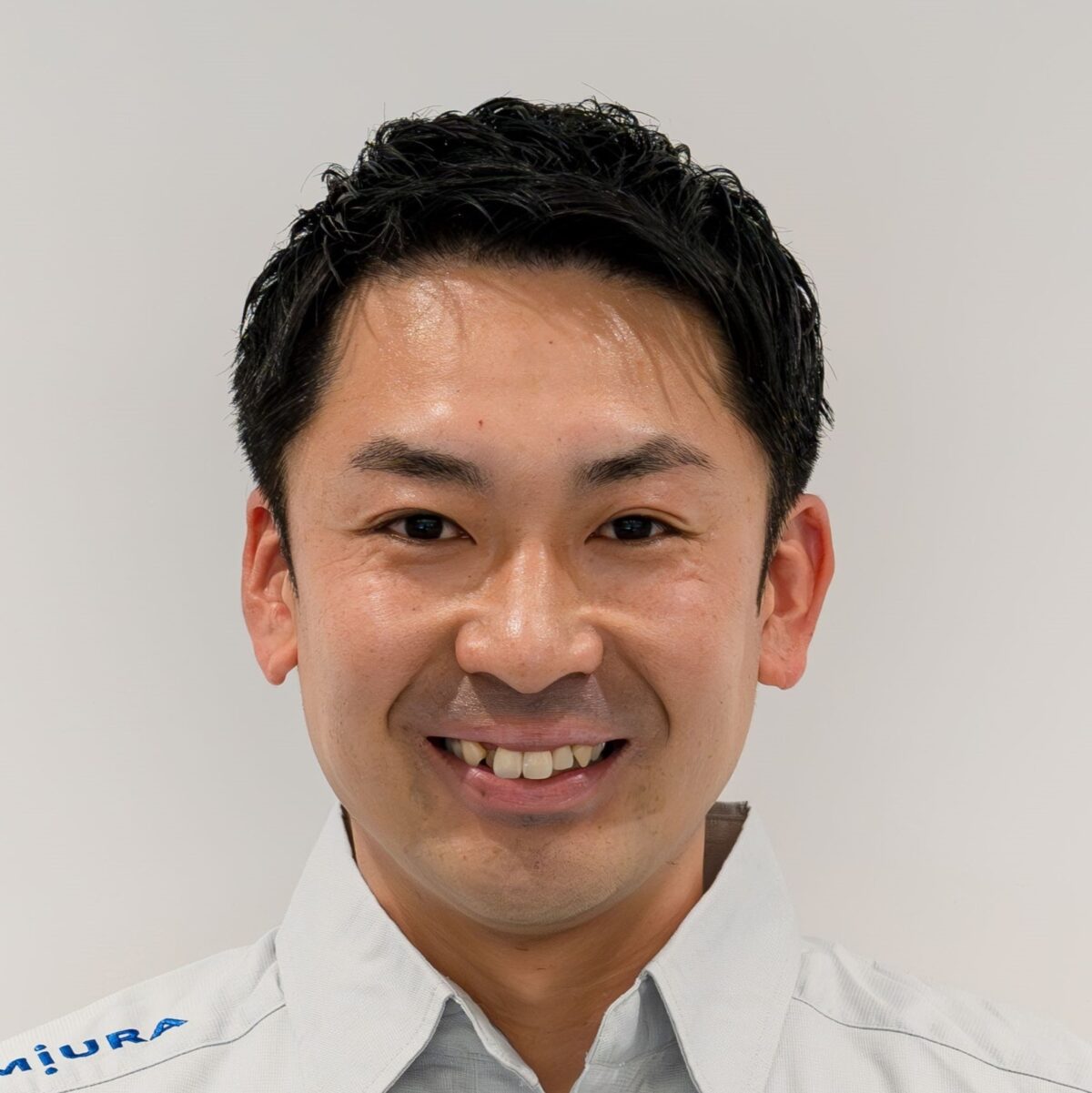
たしかにまずは、お客様から提示された必要条件をクリアすることが第一ステップですよね。
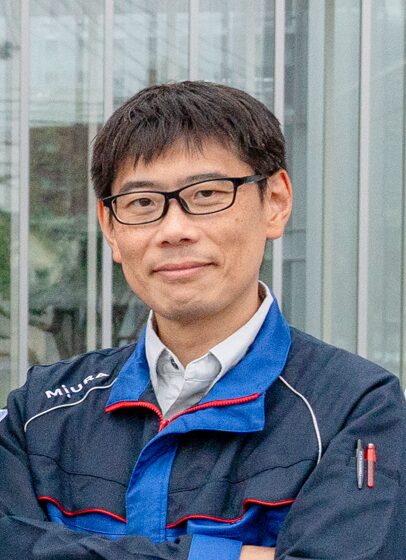
例えばSQ-2000は製品幅930mmですが、これは発売時の1990年代から変わっていないんです。メンテのしやすさを考慮すると製品幅を広げた方が作業しやすいんですけど、「ボイラの入れ替え時期がきても、またミウラ製品を選んでいただきたい」という思いがあるんですよね。そこを考えると、製品幅を合わせておく必要があるんです。なので、そこは基本的に変えないというのがルール。
でも、製品がリニューアルされると、限られた製品内部のスペースにどんどん新しい部品が追加されていく。お客様にとっては、故障しにくく、使い勝手の良いボイラにはなっているかもしれないけど、実際メンテナンス作業をするミウラのフィールドエンジニア(FE)からすると非常に作業がしづらくなってしまっているのが現実です。
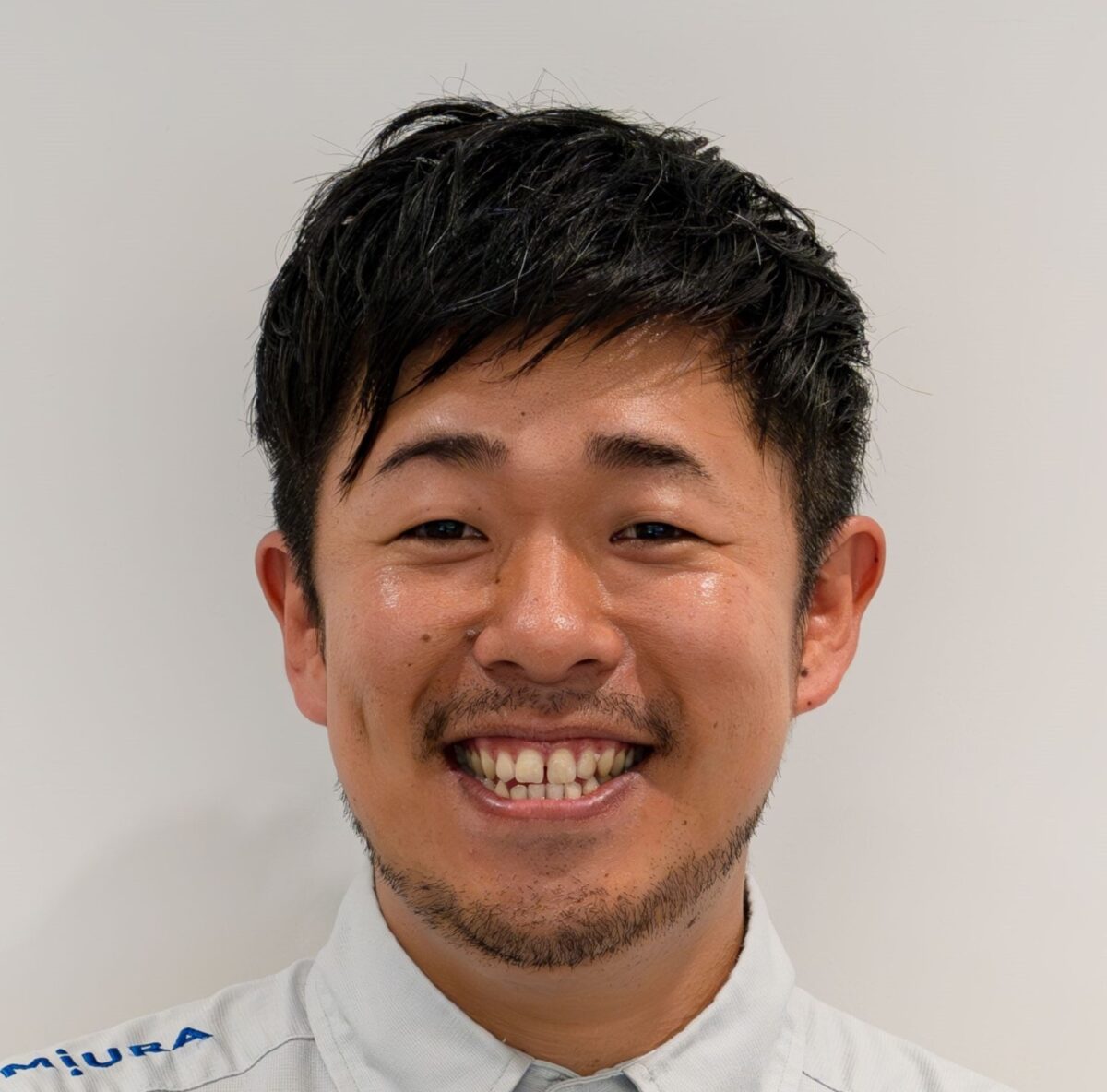
慣れてきちゃっていますけど、思い返せば、昔よりも手を伸ばせるスペースがどんどん狭くなってきてるのかも…?(笑)
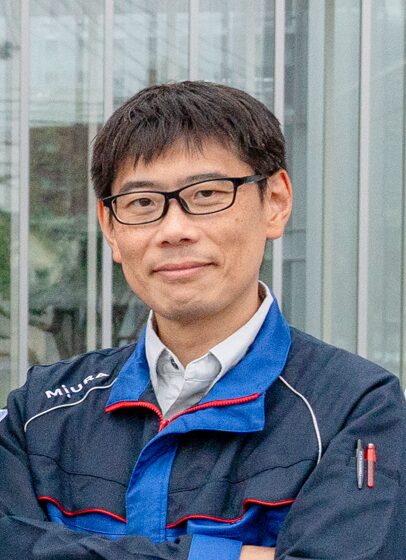
技術側でも、FEのメンテナンス性も考慮しながら、製品改良するように心がけて改善を続けているところです。
例えば、昔は剥き出しで火傷のリスクも高かった「降水管」。今は断熱材を巻くことで、省エネスペック向上と火傷防止につながるよう改善した事例もありますね。
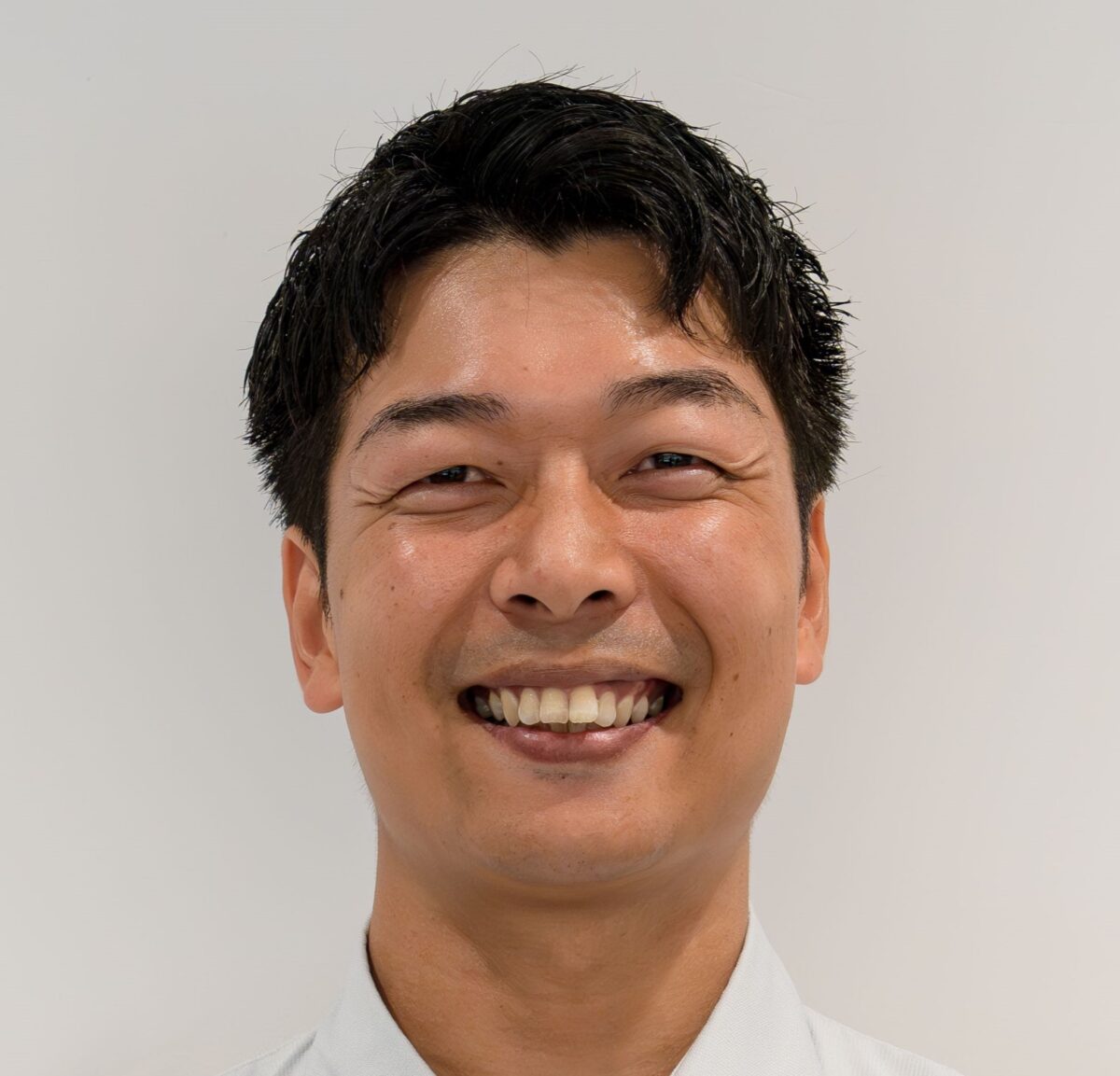
設計時にFEの意見って、反映してくれているのでしょうか?
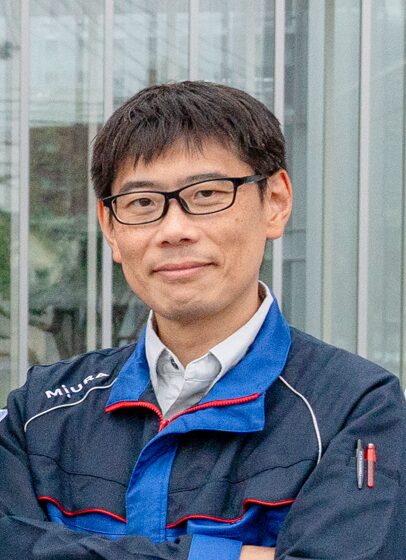
もちろんです!今ちょうど、新製品の開発に取り組んでいますが「簡単メンテ実現のために、現場(FE)の声をしっかり取り入れる必要がある」という話がでて、FEの意見を収集しているところです。
現在(2024年11月時点)、62名の社員から書き込みをいただいておりますが、優先順位をつけてできるだけ製品に反映する方向で調整しています。
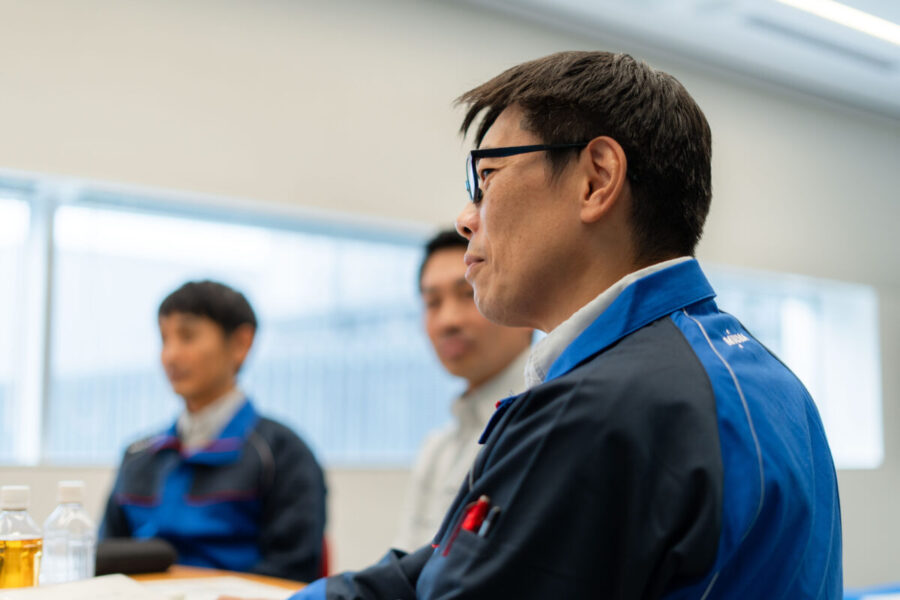
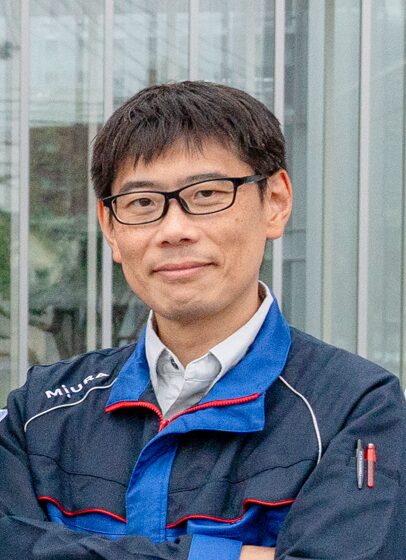
まさに、さっきまでFEの方々から届いた要望を組む設計変更の打ち合わせをしていました。数多くの要望を製品内部の限られたスペースに反映するのって、なかなか設計側も苦しい部分もありますけど…。
お客様に喜んでもらえて、かつFEの負担も減らせられる製品を作りたくて、我々も日々頭を悩ませながら設計しています。
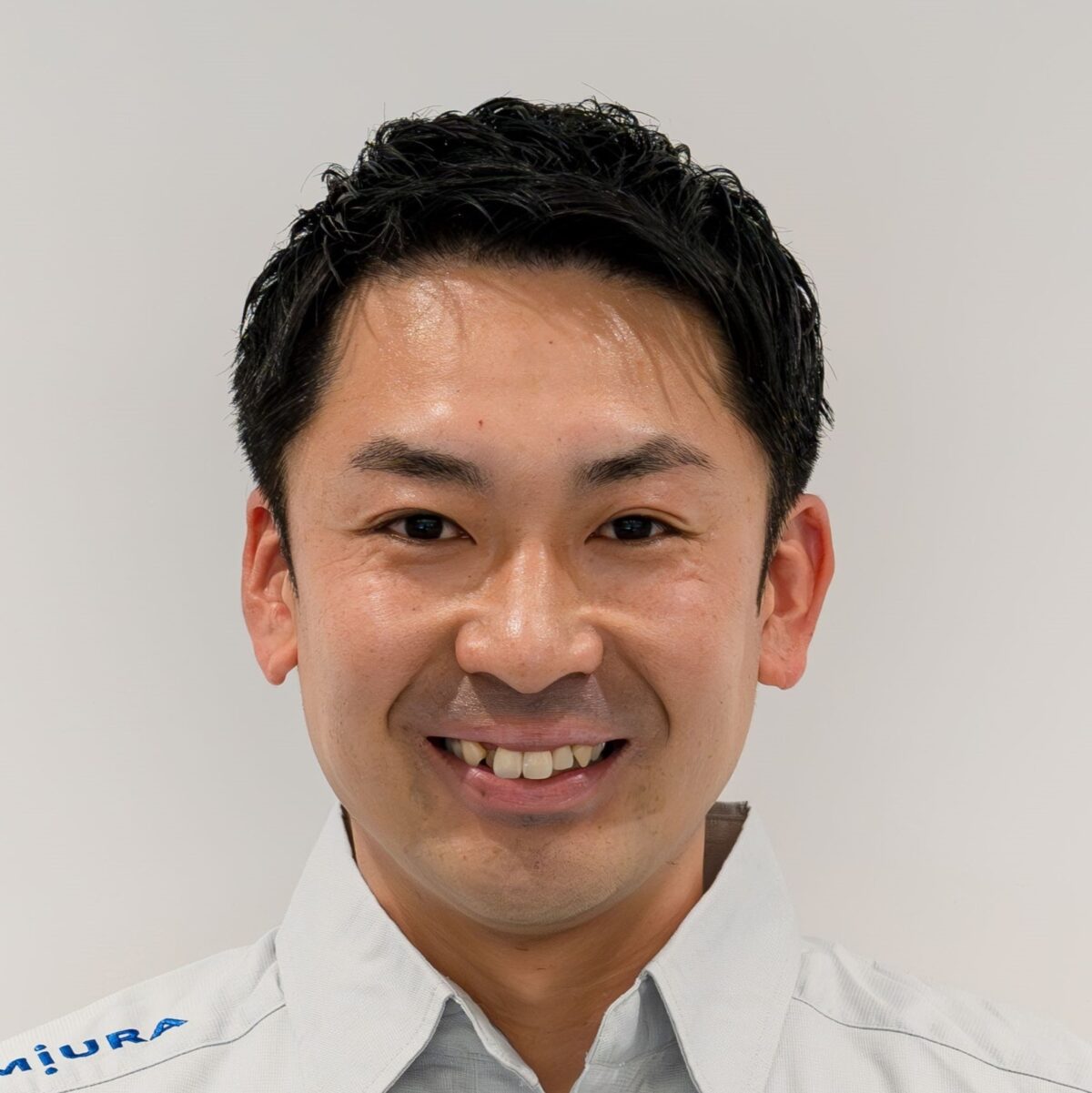
なるほど…。多彩な機能を搭載しすぎた結果、手を伸ばせるスペースが限られてきているんですね…!
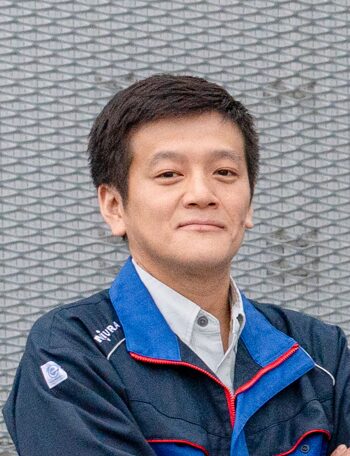
おっしゃる通りです。ボイラ効率を含む「性能」を上げるためには、いろいろな部品や機能を搭載しないといけない。でも「安全」が一番大事なので、メンテナンス時に危険が生じるような設計であってはいけない。この課題の克服が設計の仕事です。
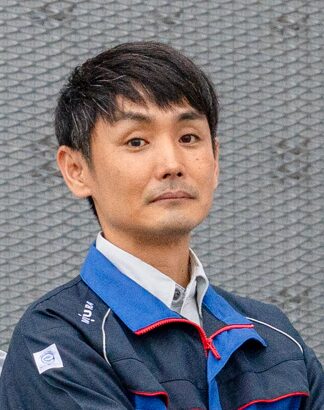
極論、何年使用しても部品の劣化がなく、故障しないボイラが作れたら、メンテナンスの必要性もなくなるんですけどね…!
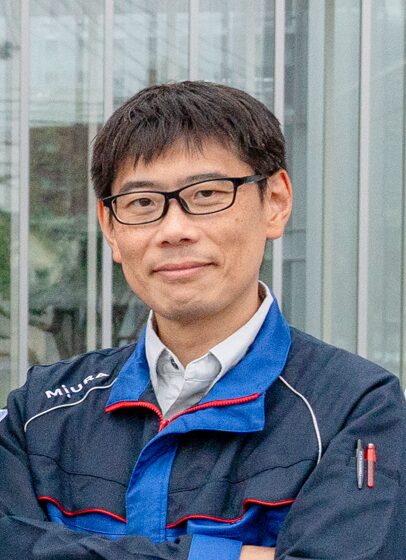
でもそれは現実的に無理だとわかっているので、現場でボイラの品質を高く保っていただいているFEの方々には本当に感謝しています。
設計者へのありがとうの声
編集部:FEの方々からお悩みの声はいろいろと聞かせていただきましたが、「改善されてよくなった」という声もぜひ聞かせてください。
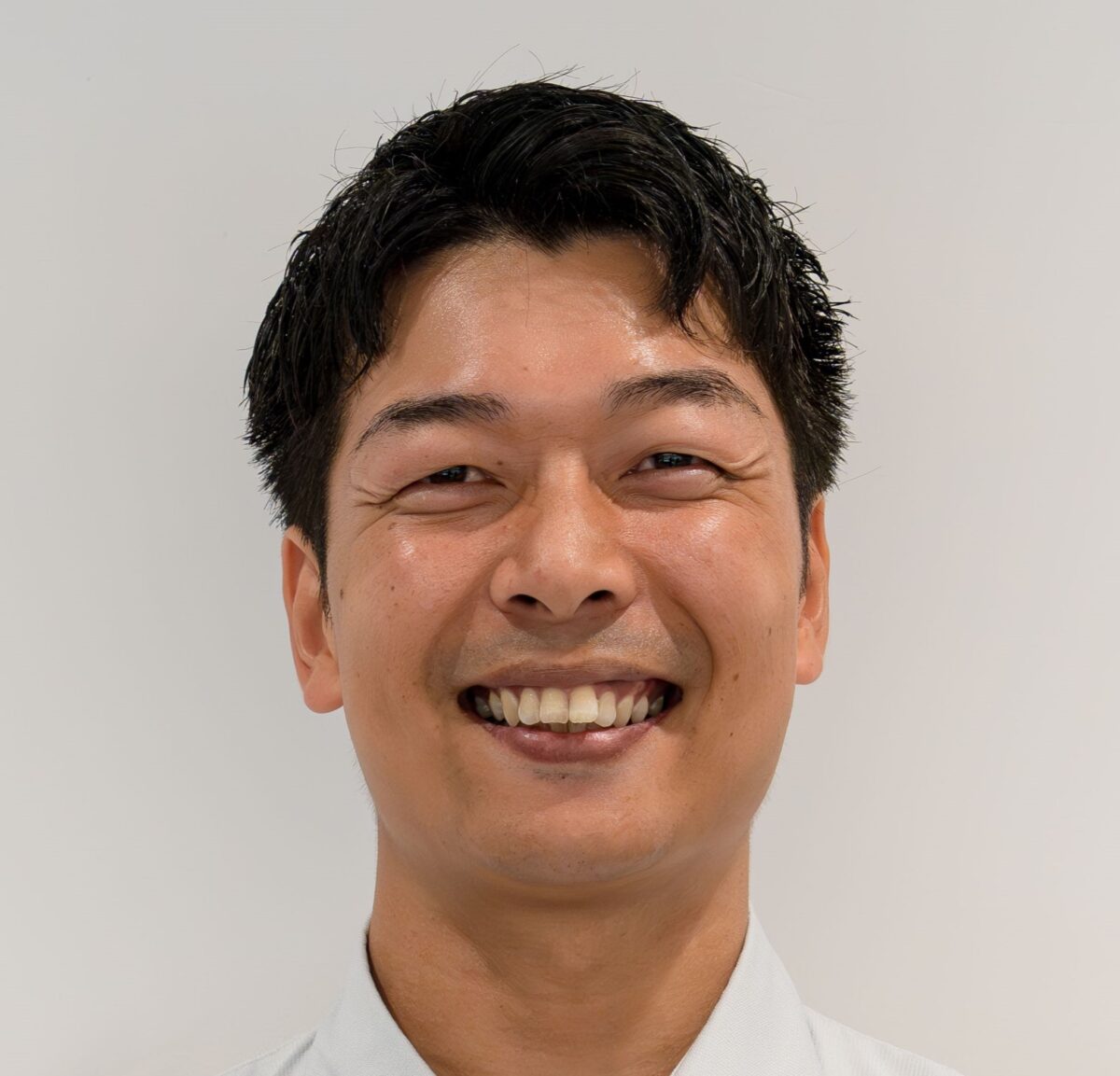
ボイラのSQ-ASにO₂センサがついたのは、めちゃくちゃいい進化だったと思いますよ!これはお客様にとっても、我々FEにとっても大きな進化でしたね。
ボイラがO₂センサで検知した数値をもとに、最適な燃焼量なるようにリアルタイムで自動調整してくれるんですよね。
損失を低減できて省エネにつながりますし、我々FEにとっても作業時間を削減できるし、たくさんのメリットがあります!
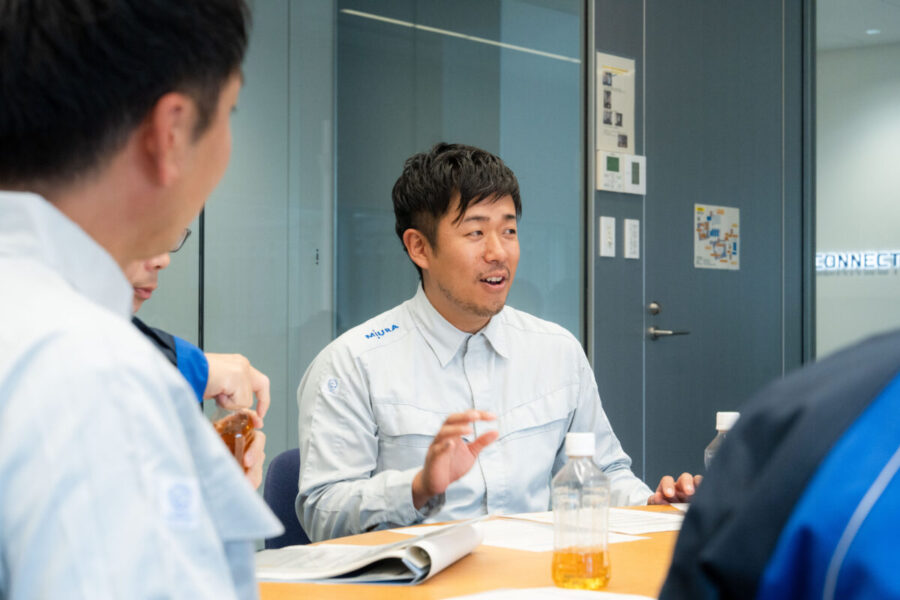
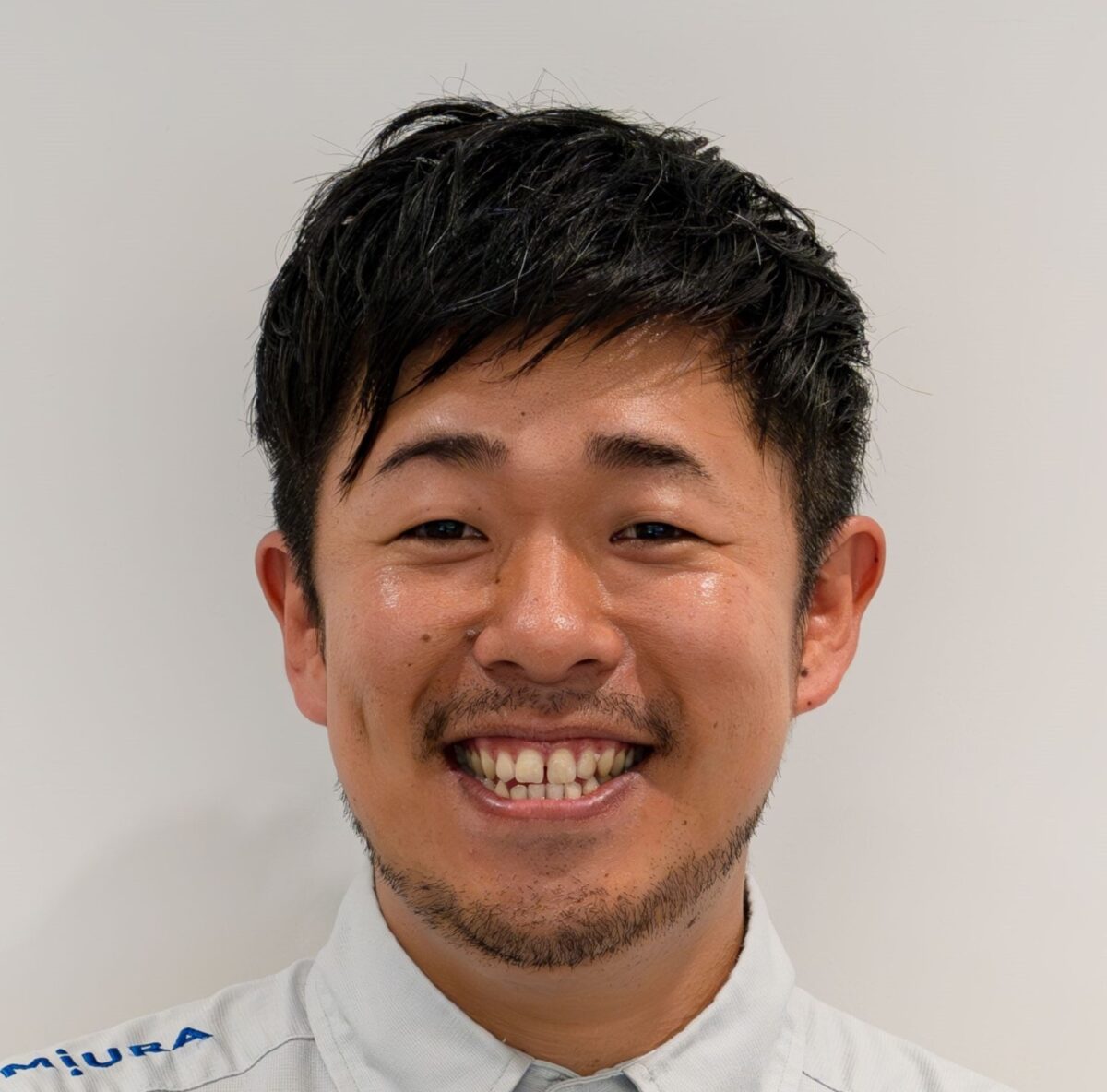
そうそう、こんなに便利でみんなに喜ばれる機能なんだから、ぜひ他の製品にも標準搭載されるといいですよね!
ほかにも、遠隔で燃焼調整ができるようになったらいいのにな~。
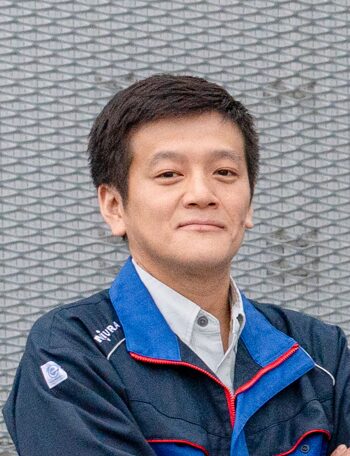
今のような「これ、めっちゃいい!」みたいな声を聞いたことなかったので、素直に嬉しいですね。
編集部:ぜひ、他にもこういう喜ばしいネタを聞かせてください!(笑)
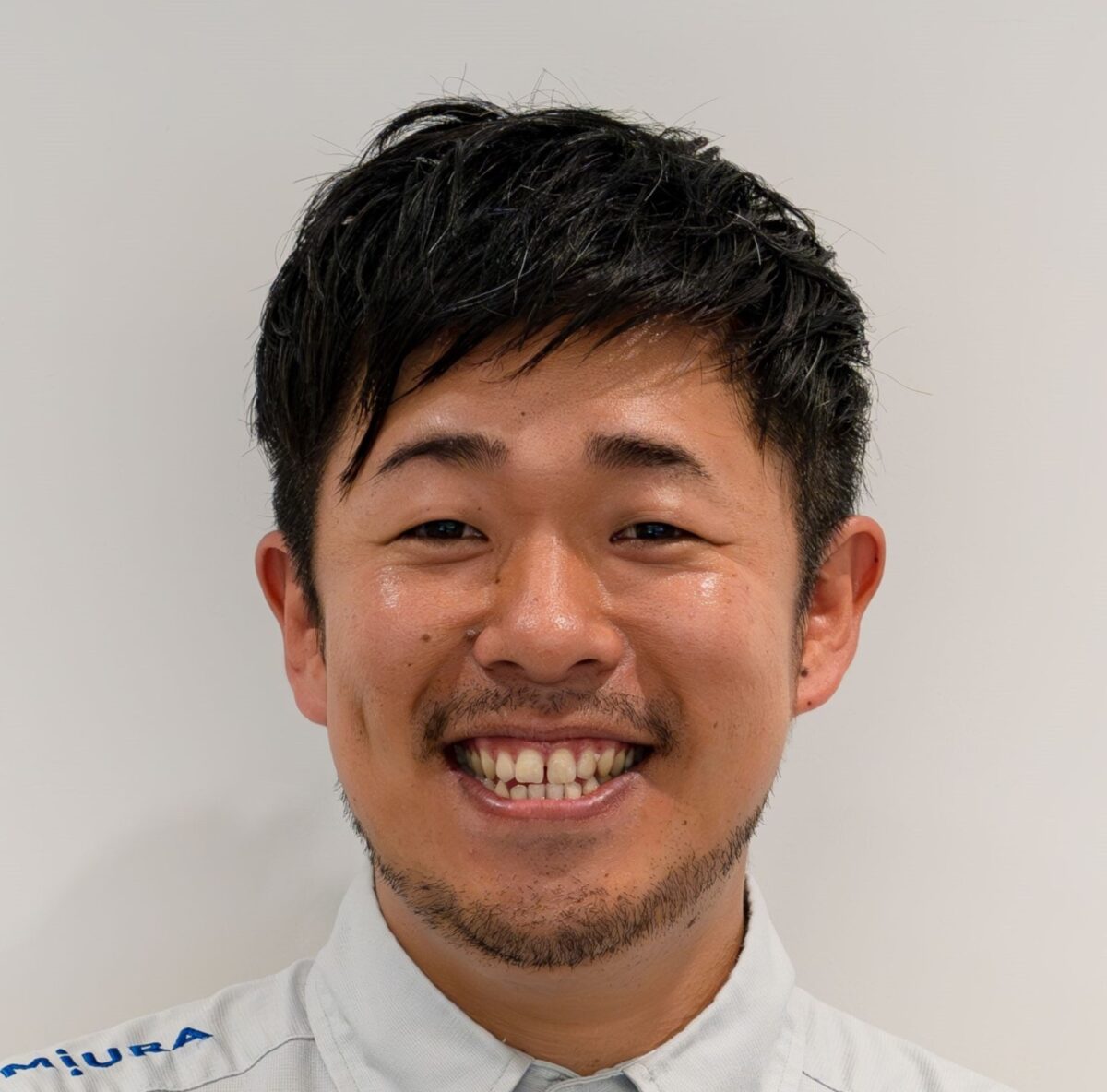
点検レポートの報告書もよくなりましたよね。以前は項目がすごく多かったんですよ。今はシンプル化されていて使いやすいです!
編集部:なるほど。こういう感謝の声って、なかなか届いてきませんか?
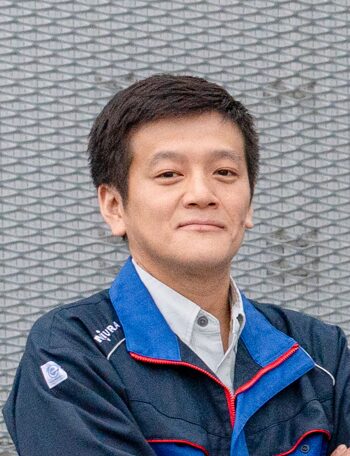
届いてこないですね。もしかしたら、そんなに「ありがたい」と思われるようなことはしていないのかな(笑)。
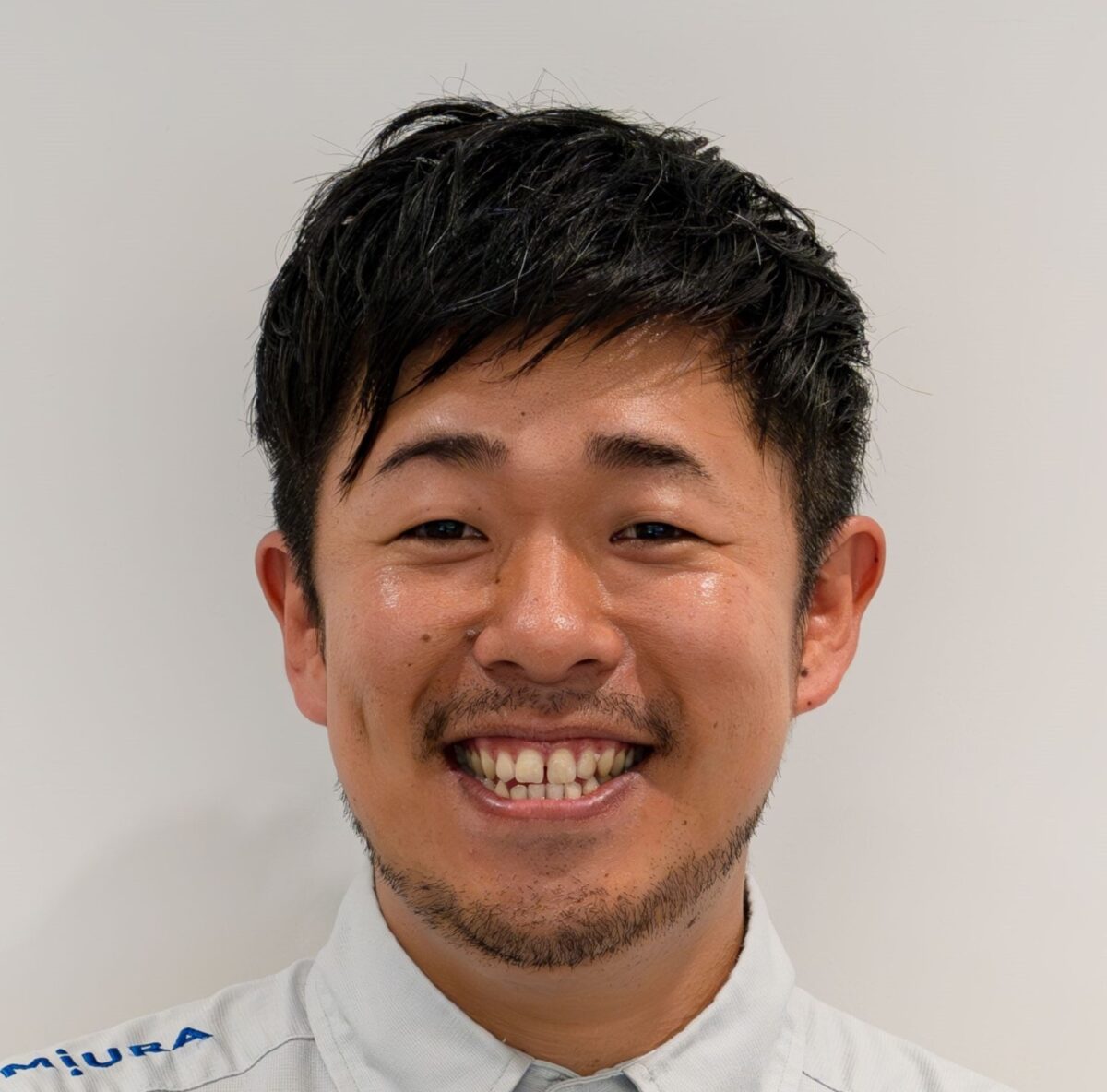
日々、製品を触っていて「この機能すごい!」と思うことは多々あるんですけど、それを誰がつくったかも分からないので、伝える手立てがないんですよね…。
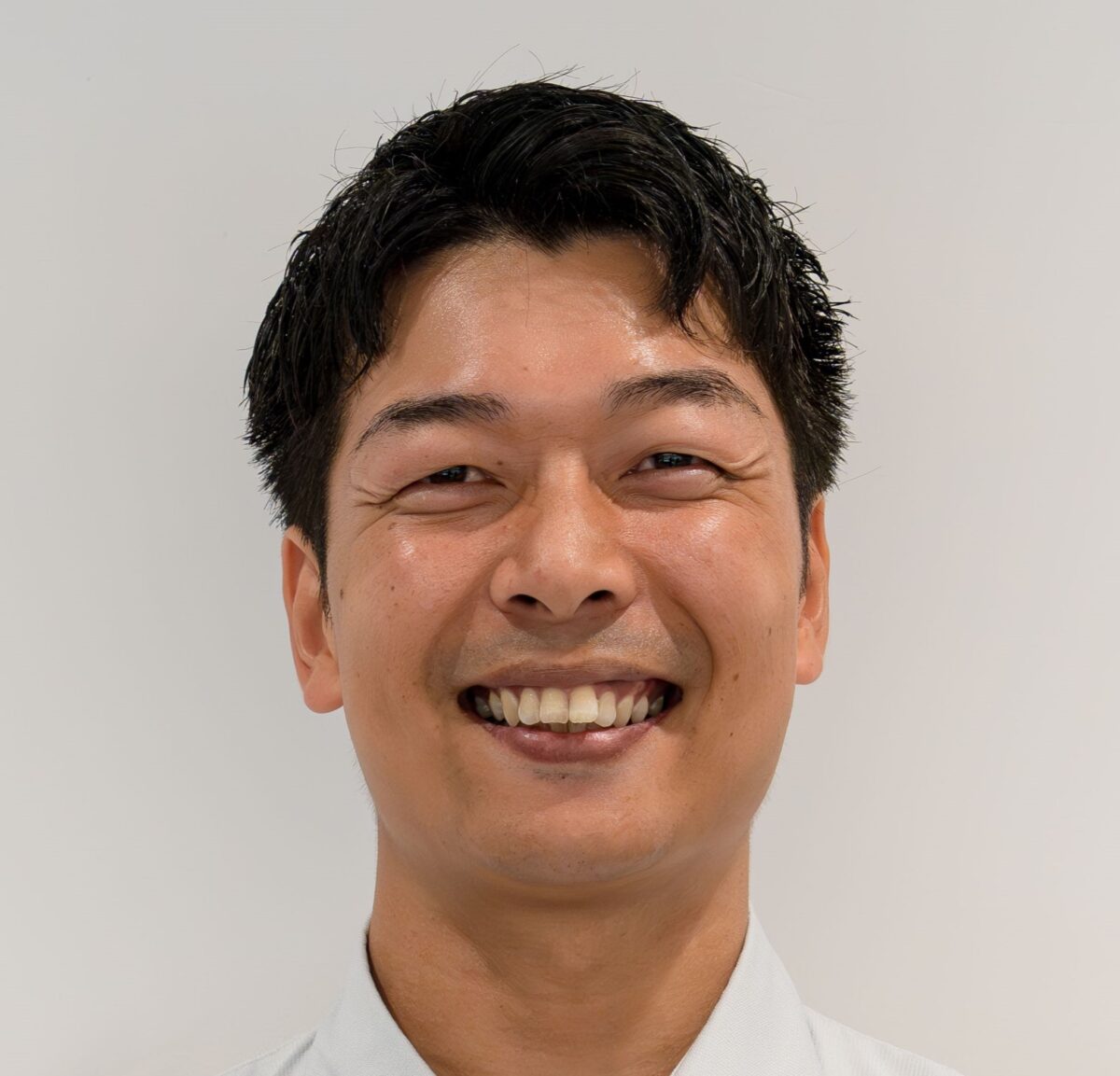
製品作った人リストつくったら、おもしろいかもしれませんね!
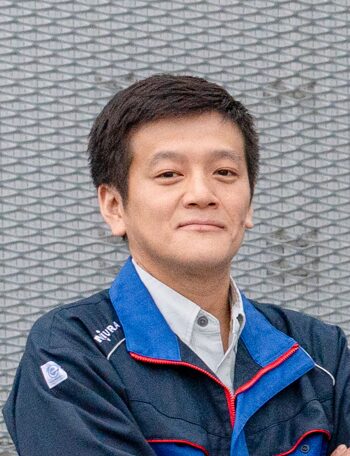
でも、少しリスクもあるよね…。「これ作ったのお前か!」みたいな(笑)
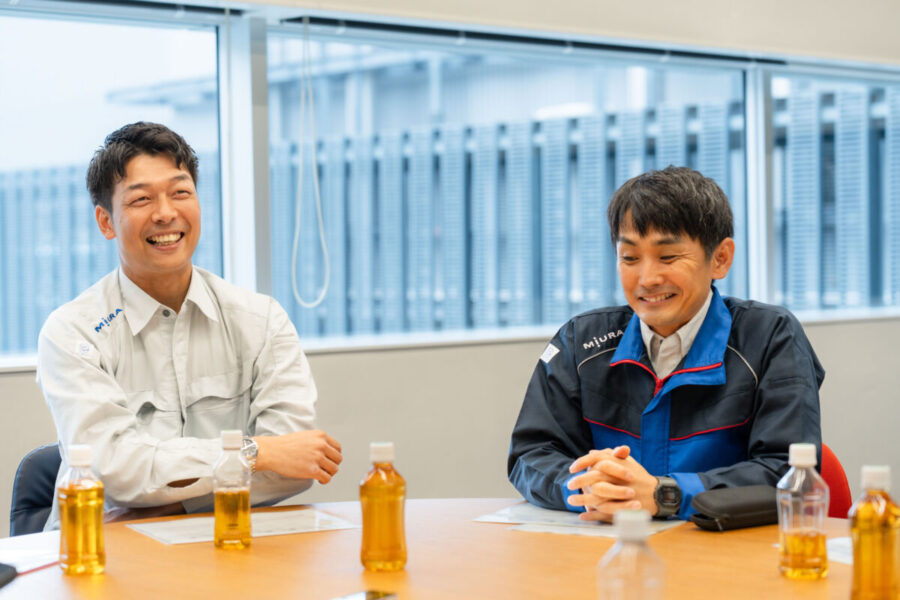
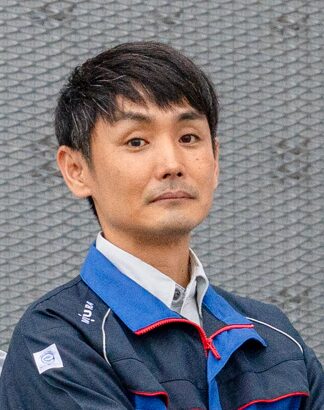
昔は、ポンプの型式など、設計者の名前の頭文字を取って付けてたみたいですよ。NVP=「苗字+Vacuum Pump」の略とか。
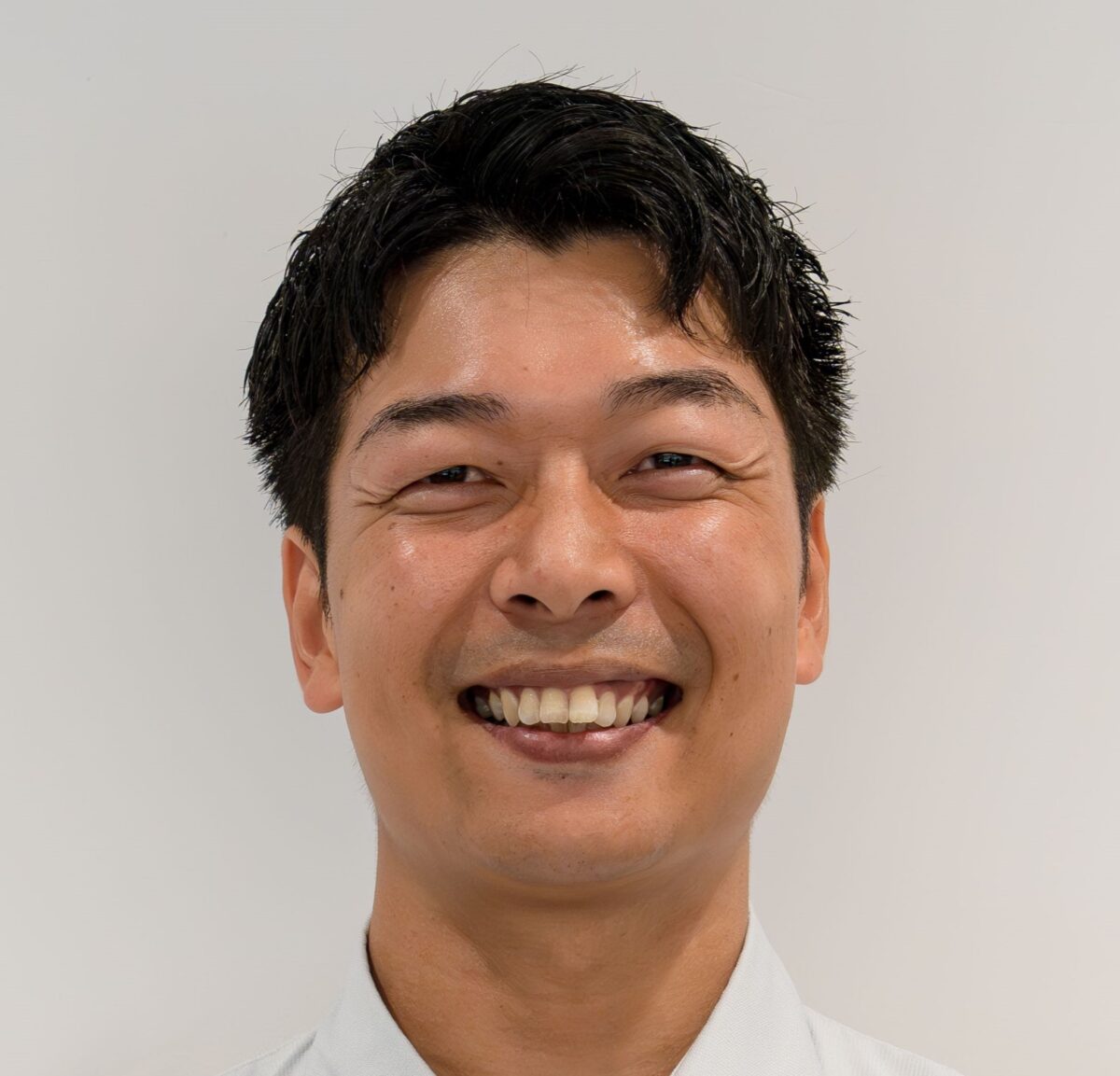
SZは鈴木さんが作ったっていう噂ありますよね?
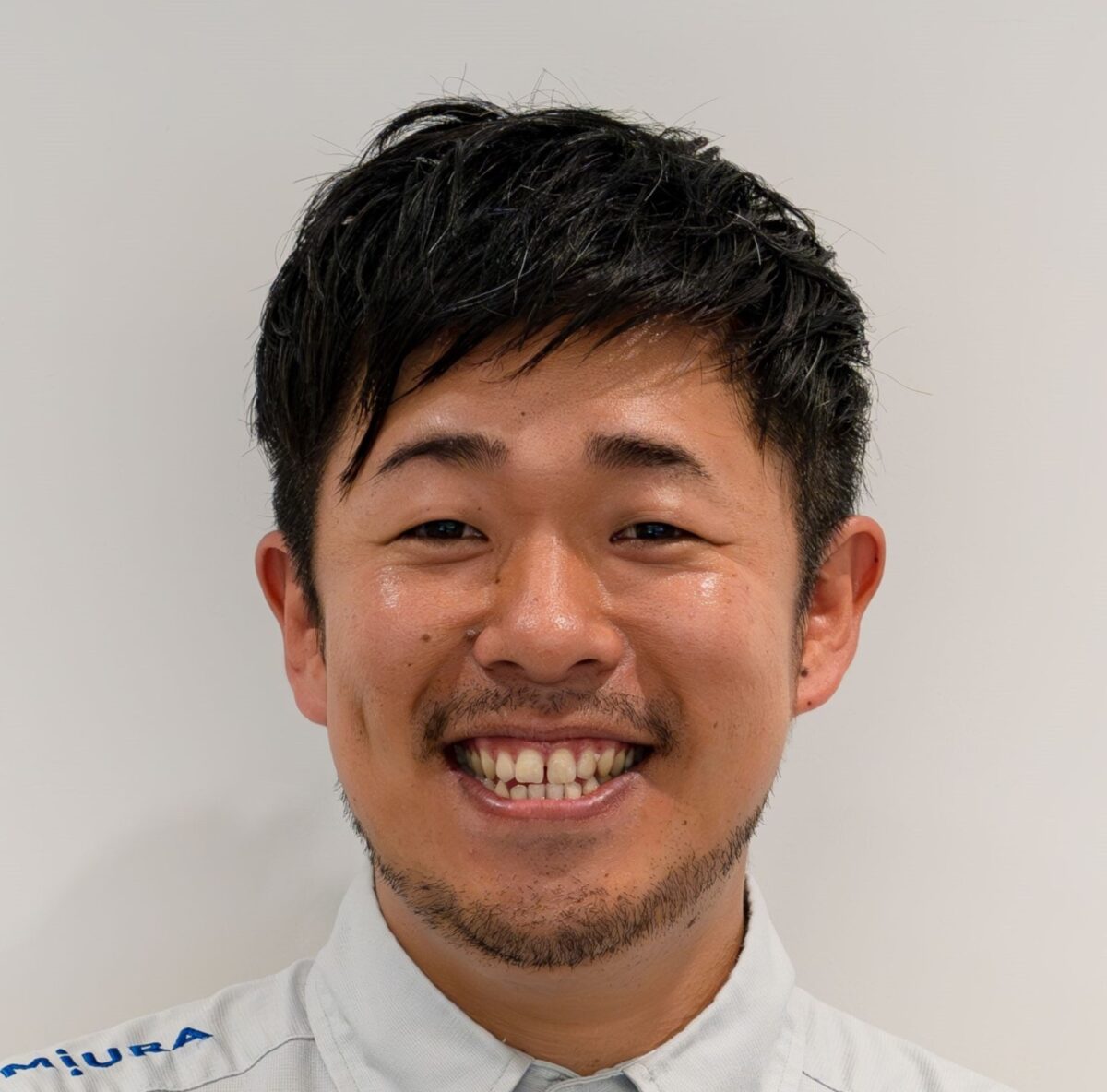
知らない。それ、どこから聞いたんだ!?(笑)
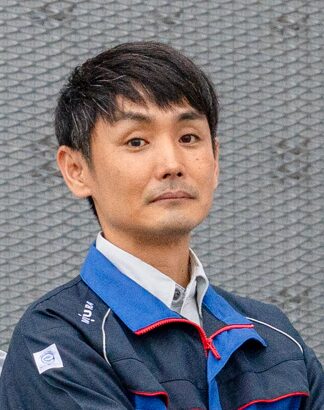
誰が作ったかの目印になるから、復活したら面白そうですね!
あったらいいな!製品開発のミライ
編集部:製品に関して「こんなものがあったらいいな!」という声はありますか?
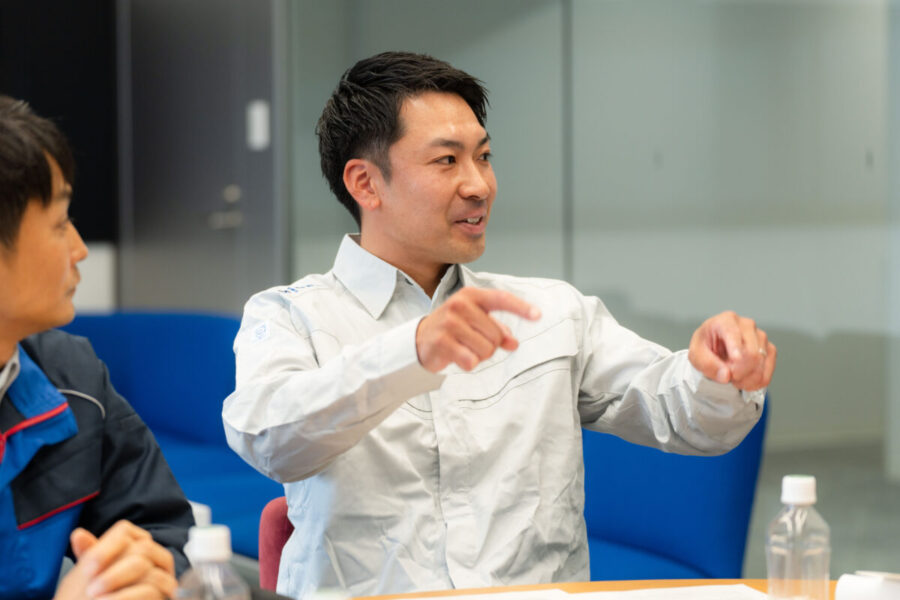
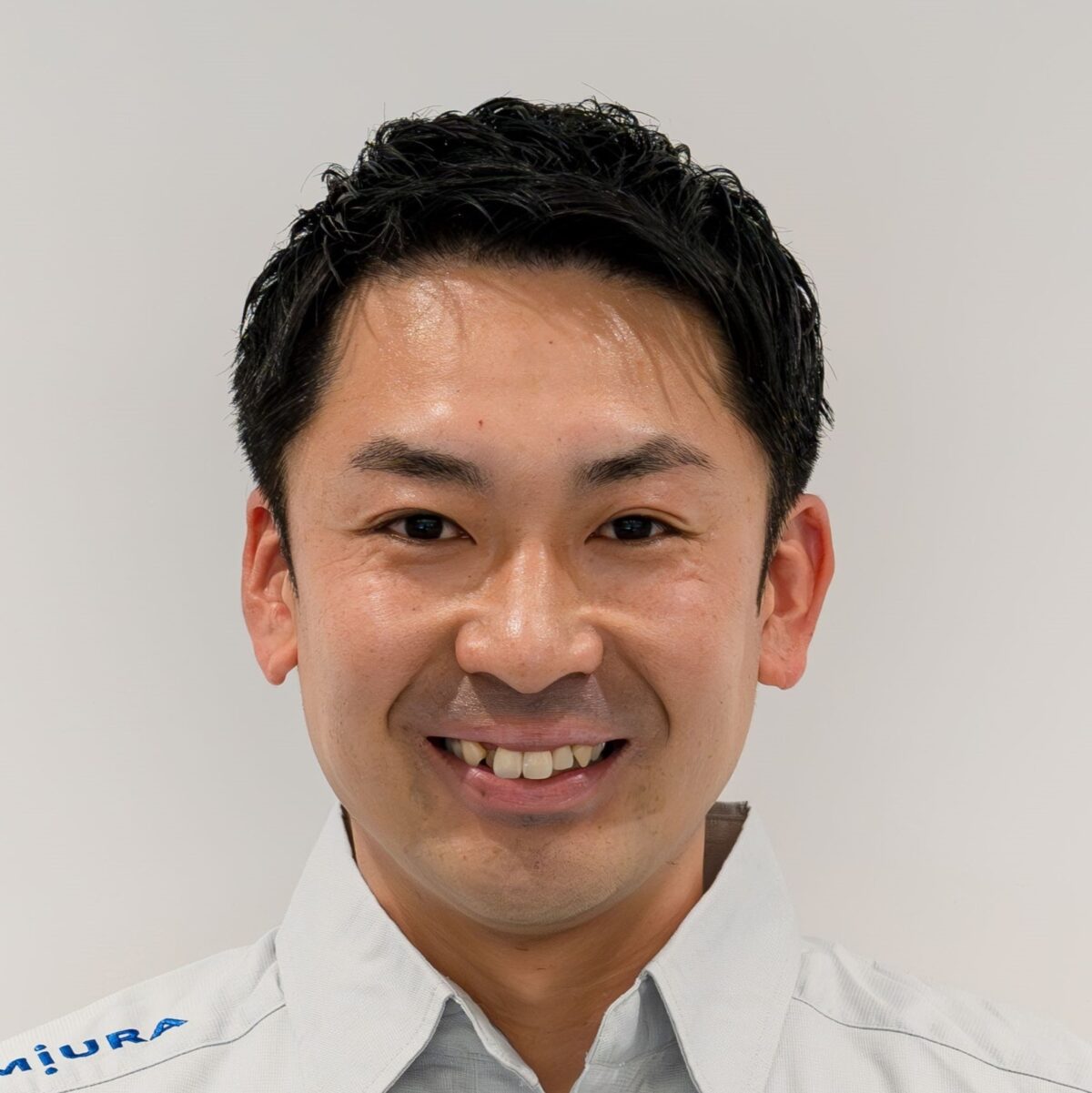
世の中には、製品の外観(ケーシング)のラッピングとかあるじゃないですか!納入先の希望に沿ったデザインで、ラッピングされたボイラ。見たことないですか?あんなのができたらいいですよね。
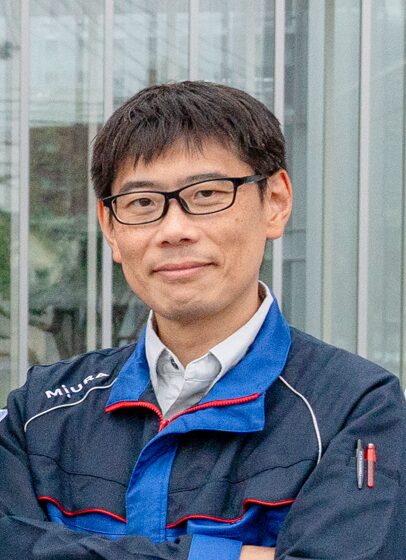
アピール用のラッピングってことですよね?特注の色のケーシング使ったり、丸型の缶体に自社商品を描いていたり…。海外ではそういうのがありましたね。
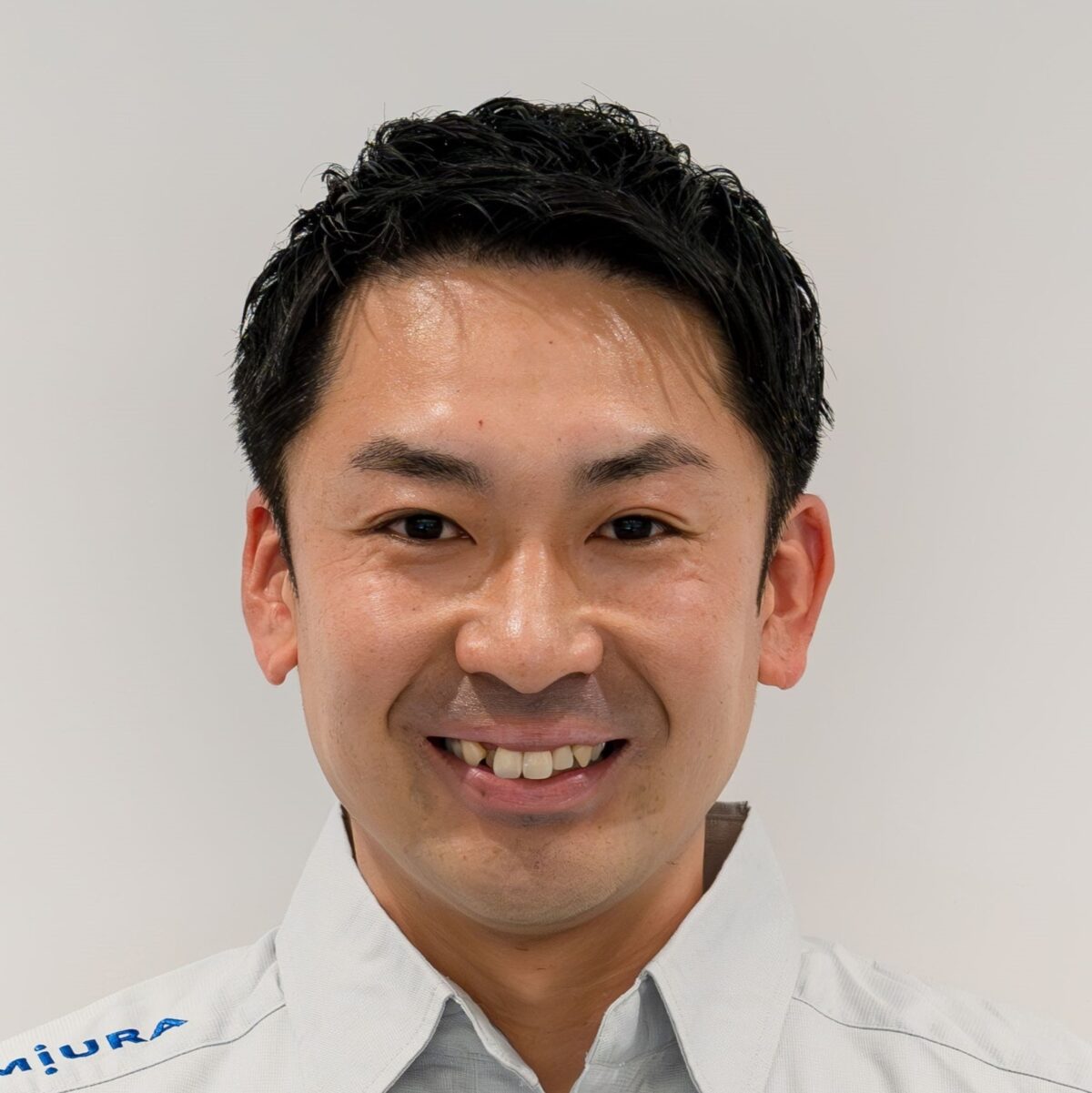
単純にお客さんが喜ぶかな〜と。実際見たことはないのですが、私の担当している地域に、ケーシングラッピングされたボイラがあるらしいんですよね。
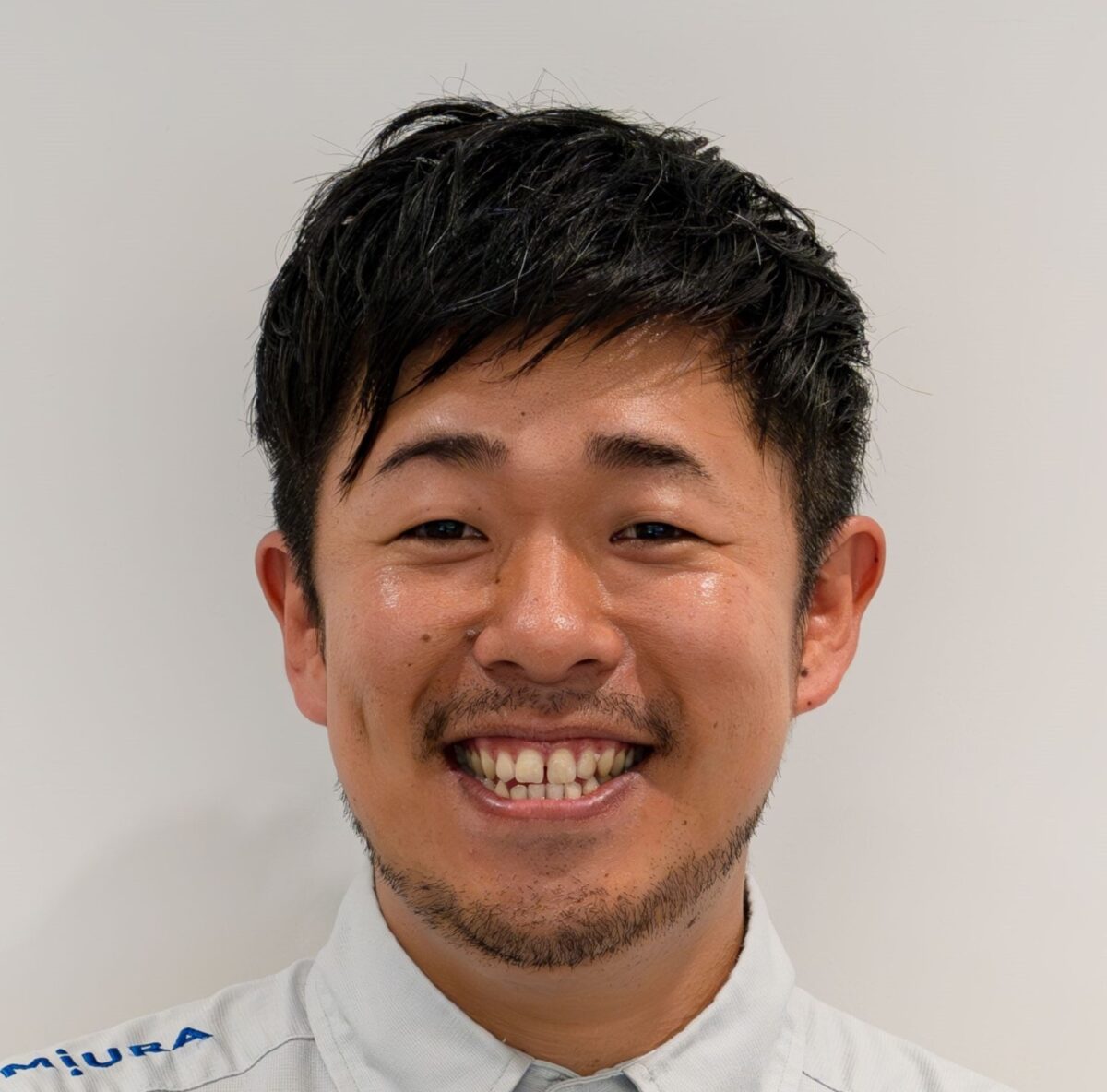
ただの産業機械が設置されてるだけじゃなくて、ちょっと愛着がわきそうですし、話題にもなりそうですね!
編集部:設計者の方々がここ数年で力を入れていることって何でしょうか?
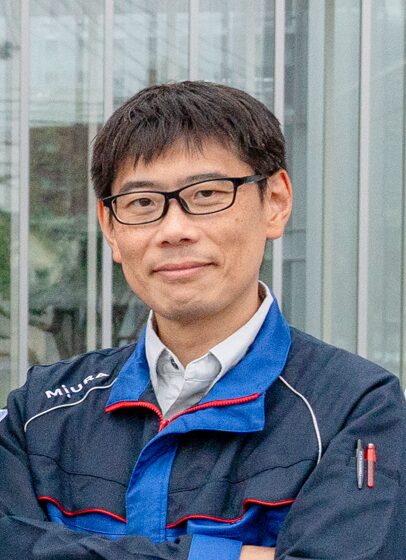
やはり、カーボンニュートラル実現に向けた製品開発ですね。
今後、どの燃料にでも対応できるように水素以外にもアンモニアなど、新燃料のボイラの開発を進めています。
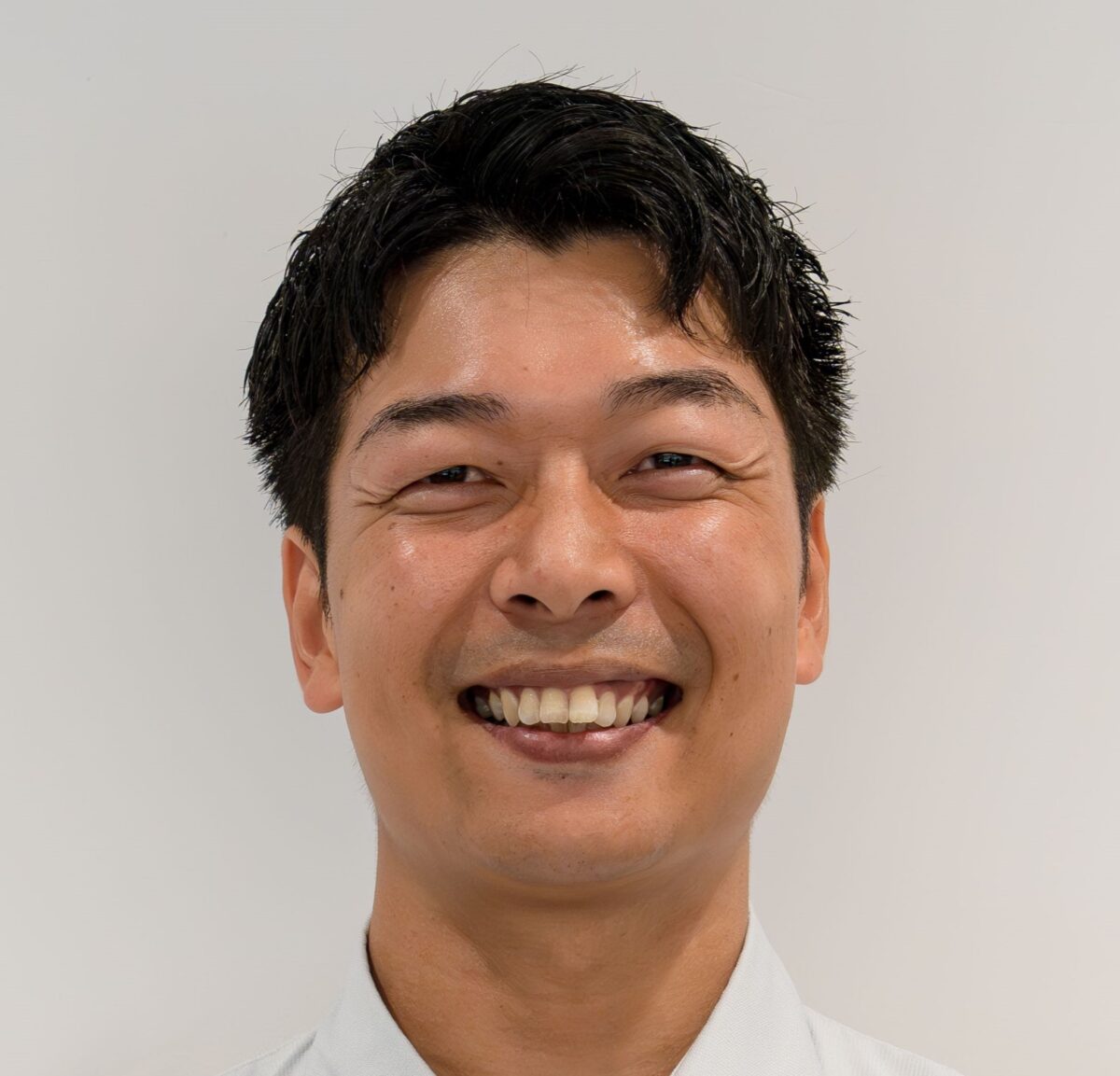
現在、ミウラでは「水素燃料ボイラ」も販売していますが、世間一般的には水素供給はこれからなので、副生水素が発生する業界でしか活用できないのが現状ですよね。
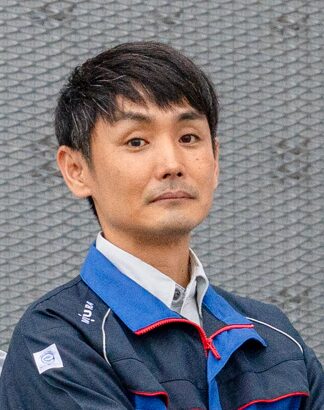
インフラ的には、水素・電気・アンモニアなどいろいろありますが、まだどれがよいかも世の中的に定まっていないので、全方位戦略で何が来ても対応できるように準備しています。
新製品開発の時は、他社が先に特許を取っていたら手を付けられないので、先手を打って取り組む必要があるんです。
編集部:世界中でカーボンニュートラルに向けた取り組みが進み、各企業もCO₂削減目標を掲げて必死に取り組んでいますもんね。これからのミウラの製品開発にも、乞うご期待!です。
設計者に聞く!素朴な疑問とモチベーション
編集部:FEから設計者に、ぜひ聞いてみたい話があるそうですが…。
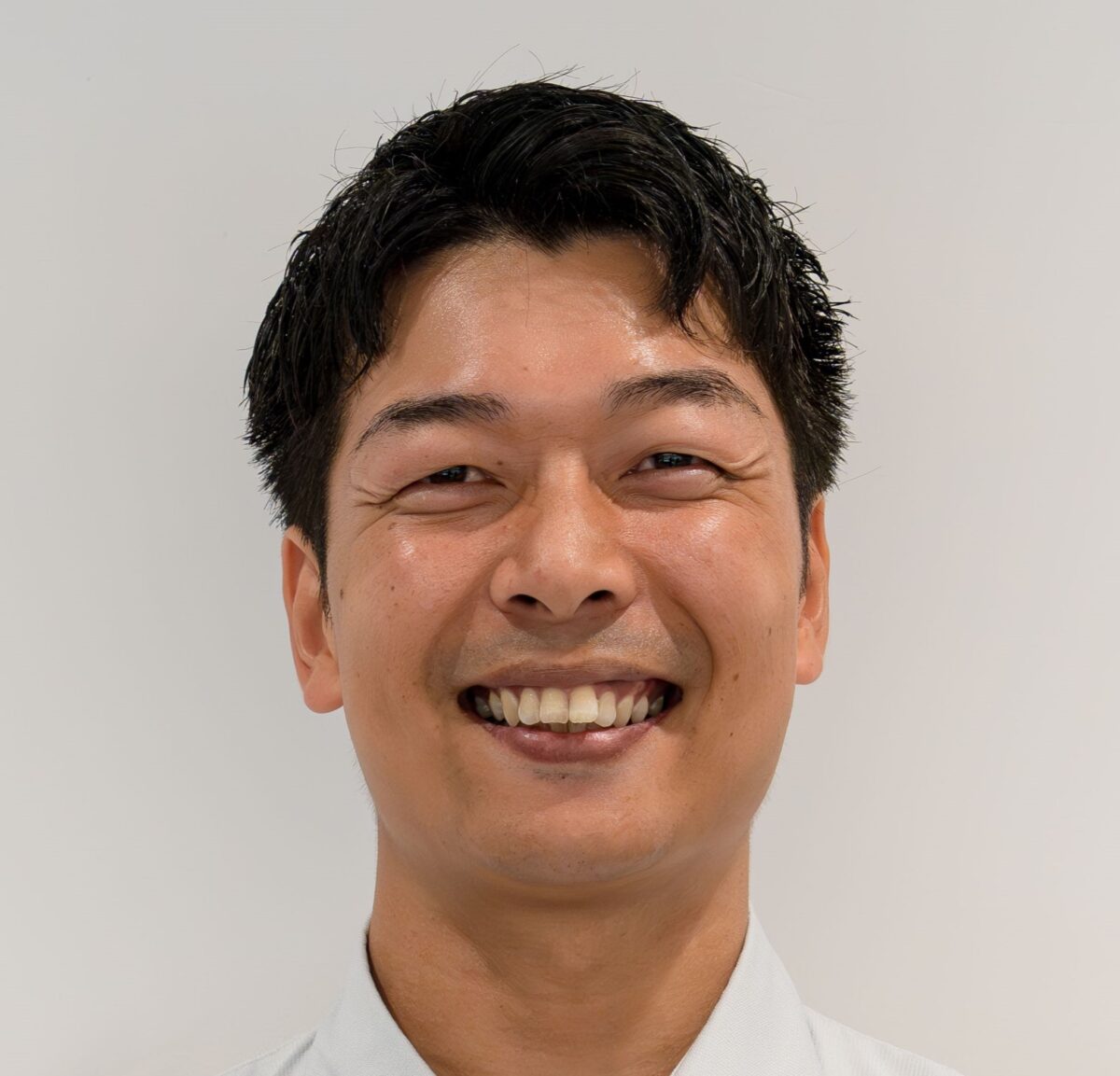
設計者の方々って、メンテンナンス作業を一通り行ったことはありますか??あの…決して煽っているわけではなくて、素朴な疑問です。
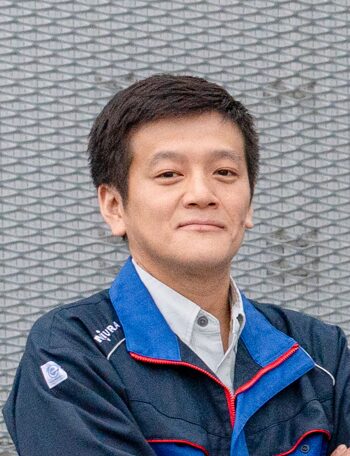
私は、入社後の研修でのメンテナンスくらいしか経験がなくて…。
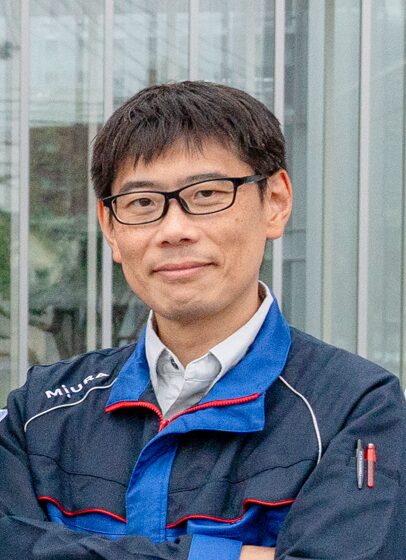
何回かメンテナンス現場に行きましたけど、真夏日だったこともあって…。とにかく暑く、FEの方々の大変さが身に染みたのを覚えています。
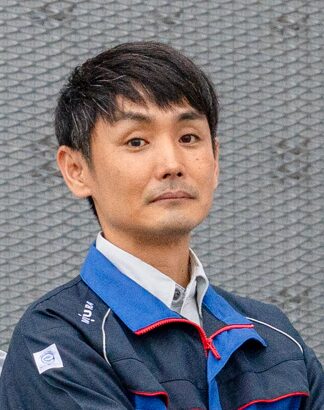
私は、設計者→FE→設計者という経歴でして、約6年間、FEを経験しました。やっぱり現場での経験を積むと、メンテナンス性など設計時の考え方がかなり変わりましたね。
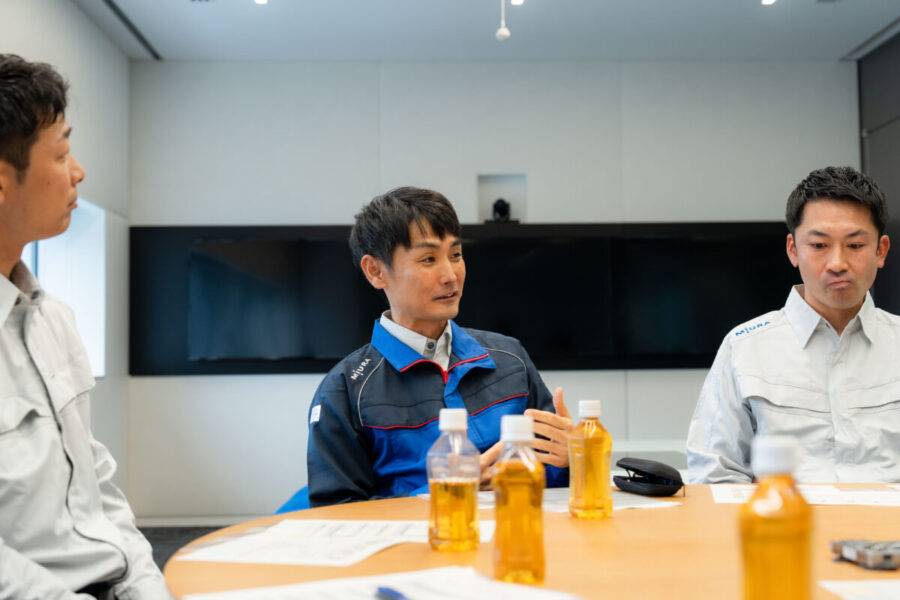
編集部:現場の様子や状況を肌で感じたうえで、製品開発に取り組むことも重要そうですね!ほかにも聞いてみたいことはありますか?
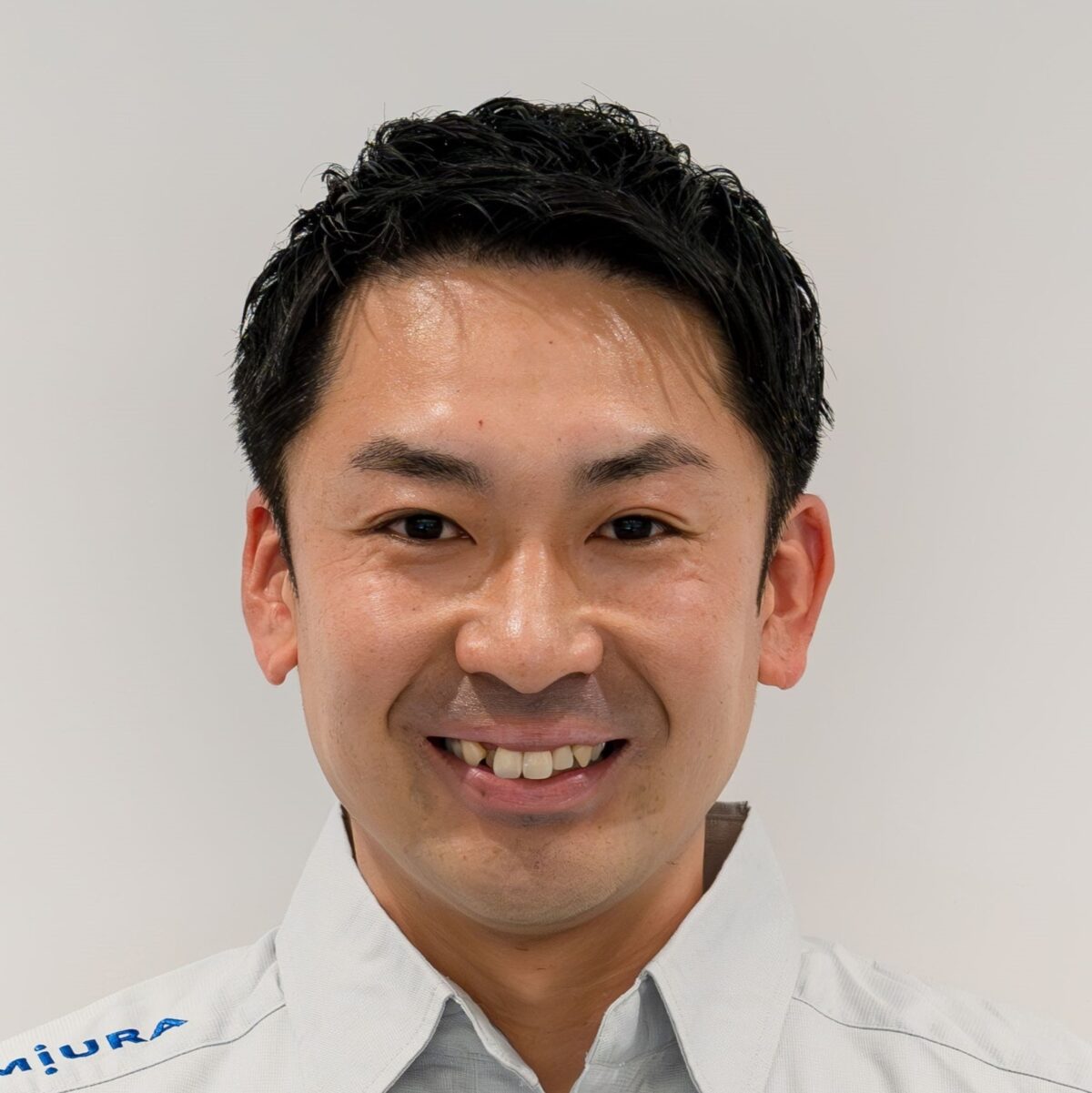
私たちFEは、お客様と直接関わるため、コミュニケーションをとったり感謝を伝えてもらったりする機会がありますが、技術者の方々のモチベーションってどこにありますか?
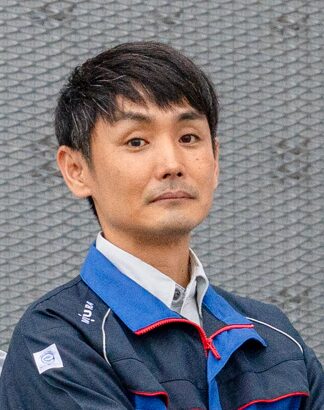
私は、新製品を完成させたときですかね。それ以外にも、「品質向上」や「改善」というテーマをきちんと反映できた!という実感があると、すごく達成感があって嬉しいです。
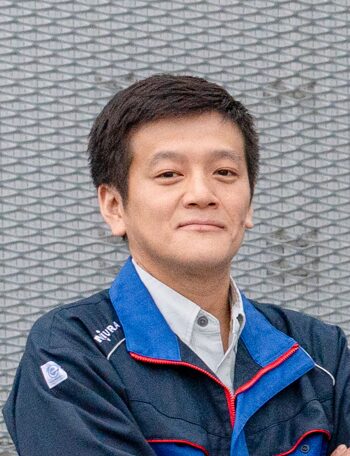
私も同じですよ。「良くなった」という実感は嬉しいです。ただ「良くなった」かどうかって、判断がちょっと難しいですけどね。
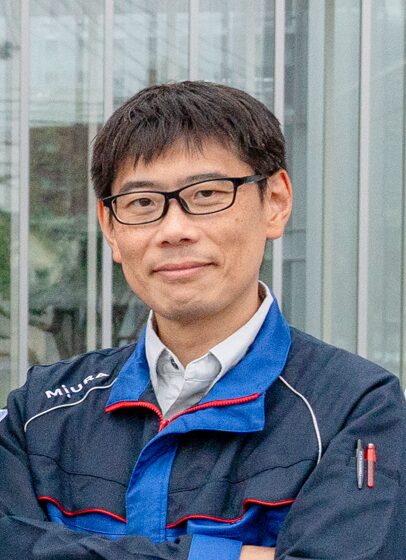
あと、私の立場としては、製品が「作れなくなること」が一番ダメなんですよね。急にモノが購入できなくなるのが一番困るんですよね。
在庫が残っている期間中に代替品を見つけてきて、複数の関連部署に声をかけて、無事に切り替えることができたらホッとしますよね。
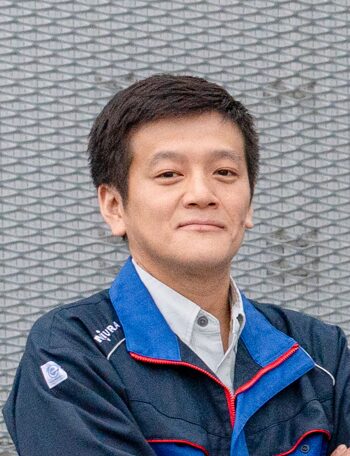
2021年頃、コロナ禍で部品が入手できない時期があったじゃないですか。あの時は必死に代替部品を探し回りました。製品の製造を止めずに乗り切れた瞬間は本当に達成感があって…。その後のモチベーションにもつながりましたね。
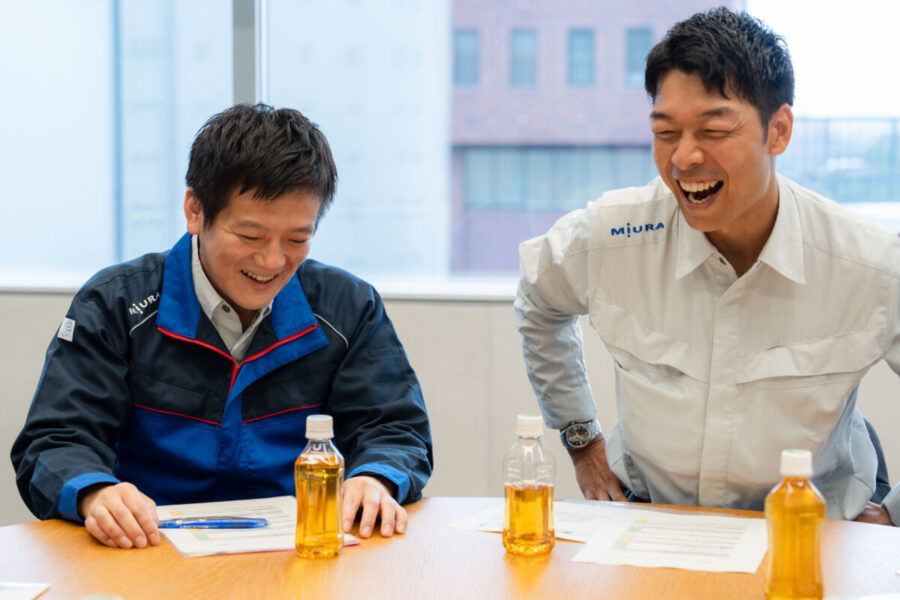
編集部:ものづくりが止まらないように陰で支えながら、会社の方向性を汲み取って未来に向かって動く。それが設計者なんですね。
そして実際に手を動かし、お客様ともコミュニケーションを取りながら、会社の軸となる「メンテナンス」を支えてくれているのがFE。
ミウラにとっては両者とも、とても大切な役割を果たしてくれていますね。
今回のように、コミュニケーションを取り、お互いに力を合わせながら、よりパワーアップしたミウラを作っていきましょう!
まとめ
座談会のあとは、実習場へ。話題に出たお互いの主張を、実際の機械を見ながら説明し合いました。「確かにこれは大変ですね…」「なるほど、こういう意図でここに設置されているんだ」など、お互いに納得の声や笑いが出る、よい時間でした。
密接な繋がりがありながらも、なかなか直接交わる機会がないFEと設計者。今回、とても充実した意見交換ができたと思います。
今後も、ミウラの同志として、感謝の声を伝え合い、相互理解を深められるような交流ができる仕組みが整えばよいと感じました。
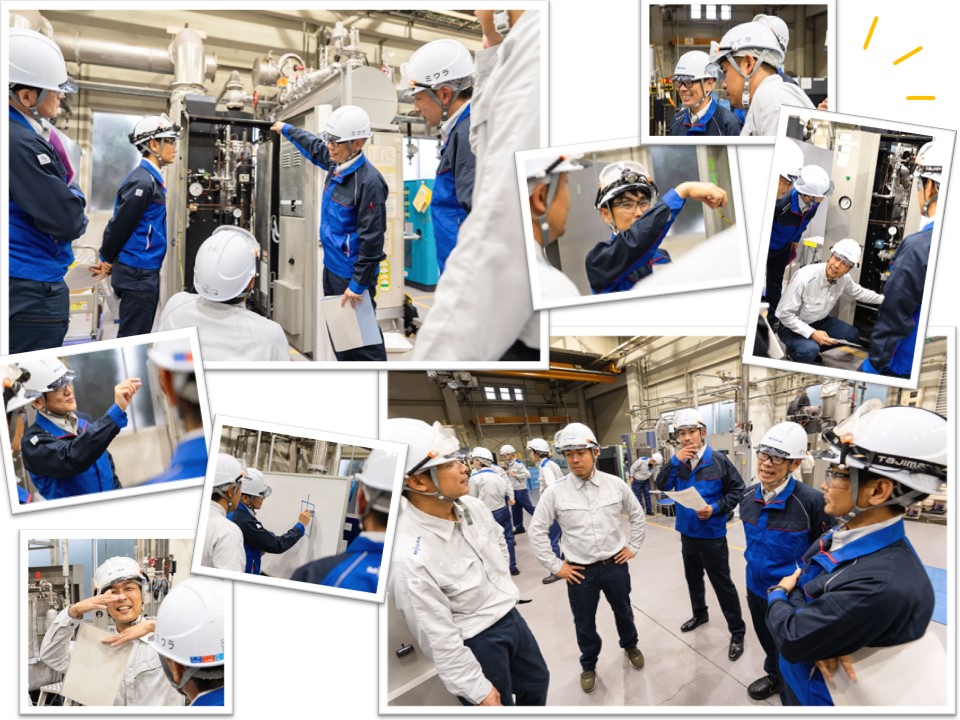
訂正履歴
文中の「最適な空気量となるように」を「最適な燃料量となるように」に訂正いたしました。
(2025年3月4日)