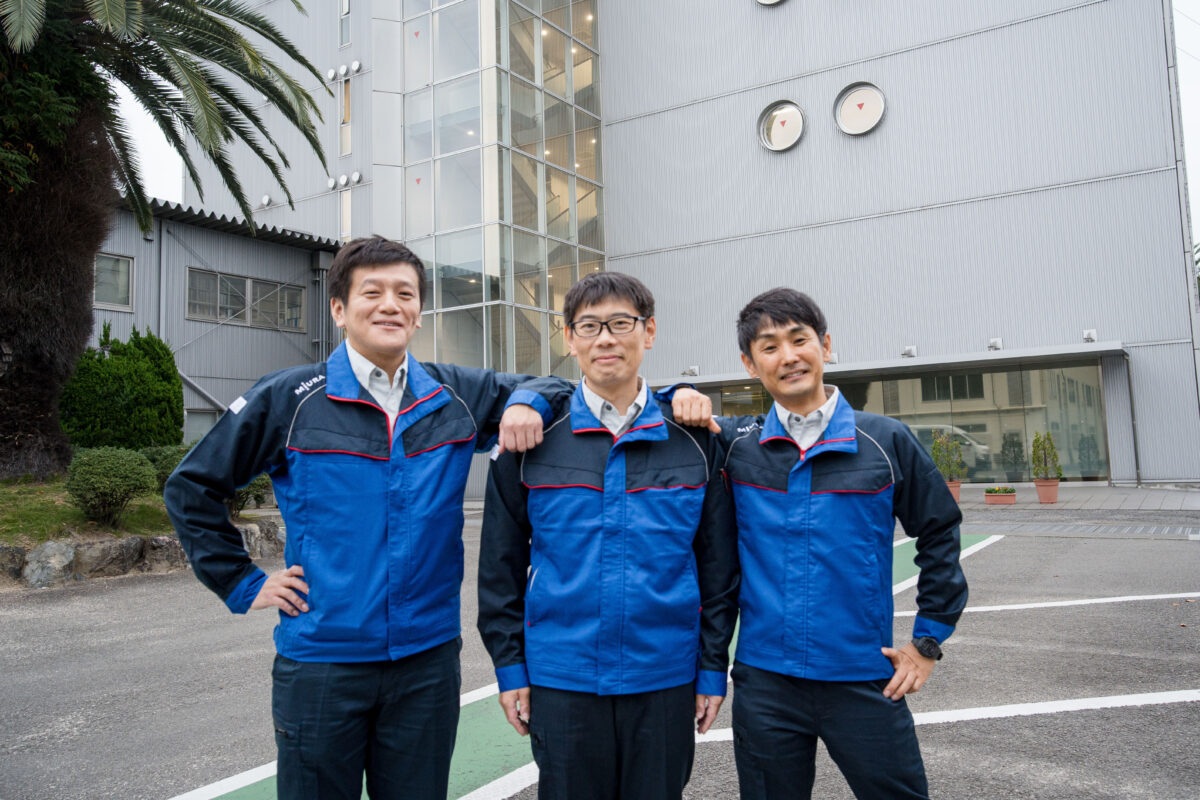
設計者のキモチ 〜安全性・品質・コストetc…葛藤しながらやっています〜
お題は、『設計者の思い ×FE(フィールドエンジニア)の思い』。
製品を設計する側・製品をメンテナンスする側…と密接なつながりがありながらも、なかなか直接意見交換をする機会がないFEと設計者。
2回目は、設計者の声を集めました。
前回のFEの意見へのアンサーはあるのか!? 仕事で大事にしていることや、現場に対する思いも聞きました。
島根・鳥取のスタッフが考える、次のミウラplusの企画は?! 【ミウラplus 出張編集部会議@山陰 part3】
MENU
part1 わかって欲しい!メンテナンスの苦労と努力
~フィールドエンジニアたちの本音編~
part2 設計者のキモチ
〜安全性・品質・コストetc…葛藤しながらやっています〜
参加者プロフィール
かみや よしてる
神谷 佳輝
KAMIYA Yoshiteru
ものづくり技術部 ものづくり技術課 係長
プロフィール
2006年入社。技術部量産設計課、アメリカ駐在部(5年間)を経て、ものづくり技術課へ。国内ボイラの量産維持対応を行っている。特技は数字を覚えること。
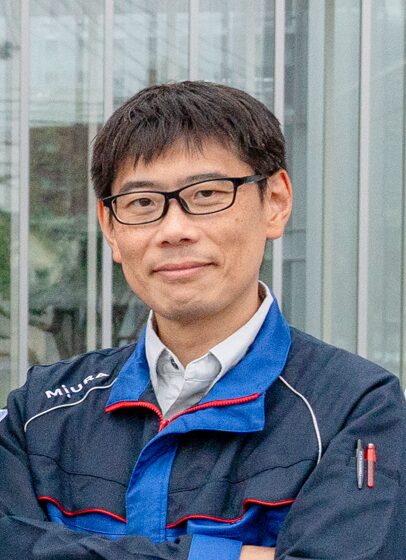
やまうち こうた
山内 孝太
YAMAUCHI Kota
ボイラ技術部 ボイラ技術課 主任
プロフィール
2007年入社。流体センサ技術部、熱機器特需部、グローバル技術部、熊谷支店(6年間)を経て、ボイラ技術部へ。標準ボイラの量産維持・品質向上を行う。単身赴任のため、家族とのTV電話が楽しみ。
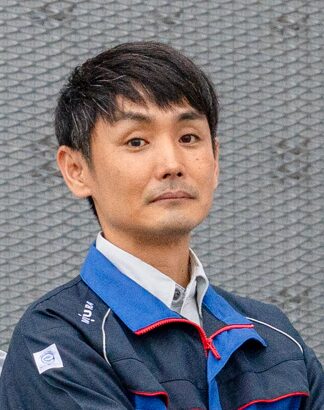
よしたけ じゅん
吉武 淳
YOSHITAKE Jun
ボイラ電機技術部 ボイラ電機技術課 主任
プロフィール
2015年入社。電機技術部、グローバル技術部を経て、ボイラ電機技術部へ。国内ボイラの電機設計、海外ボイラの電機設計支援を行う。趣味はスポーツ鑑賞(特に相撲)。
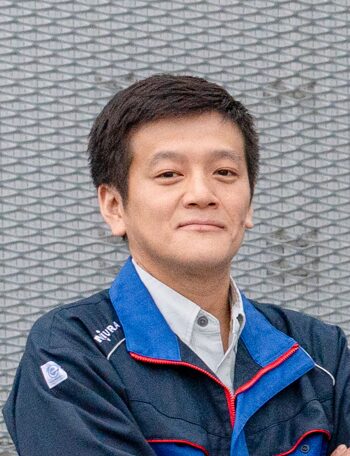
設計者の仕事とは?
編集部:設計者の方の普段の業務を教えてください。
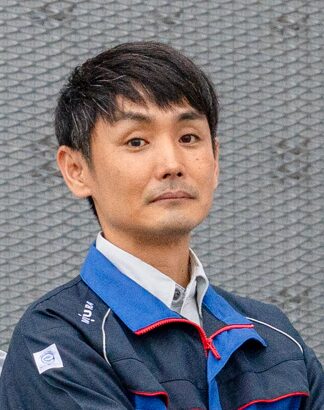
テーマに沿って設計するのが基本のスタイルです。新製品開発・品質改善などいろんなテーマで目標を立て、スケジュールを組んで進めていくのが設計の仕事。もちろん、それだけではなくて、現場からの不具合対応もあります。様々な要因で品質の基準が満たされなかったり、ボイラが着火できなかったり、毎日のように連絡が入るので、それを受け答えしながら仕事をやっています。
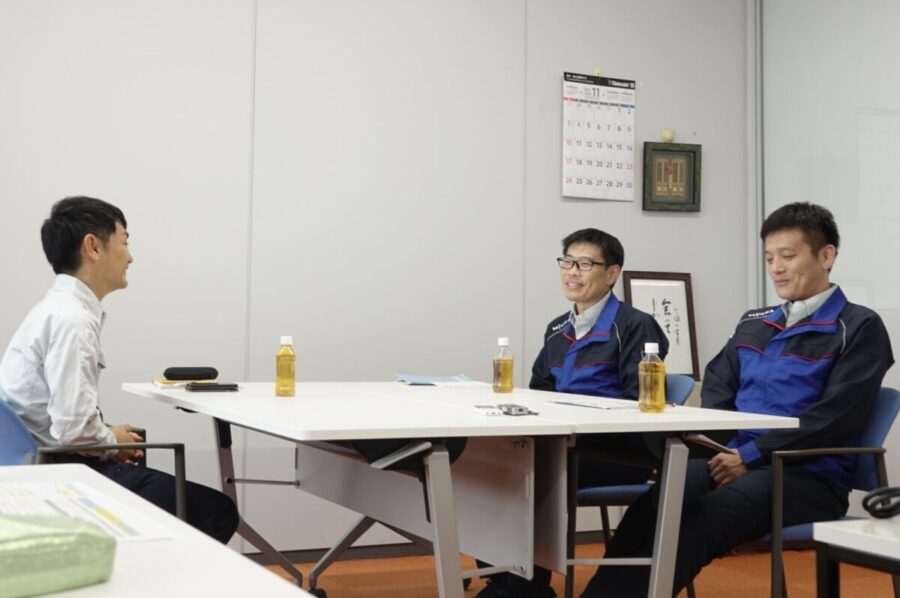
編集部:「現場の不具合」の声は、どこから届くのでしょうか?フィールドエンジニア(FE)からですか?お客様から直接ですか?
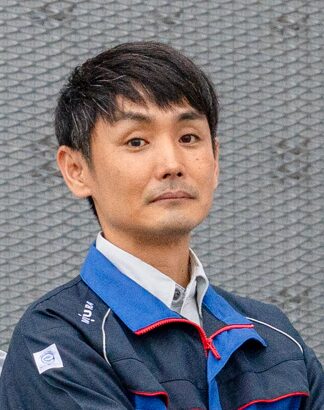
通常の流れであれば、FEと設計者の懸け橋となる”メンテ技術部”を経由して現場(FE)の声が届きます。できるだけ窓口を一本化して案件を割り振ってもらっていますね。問い合わせ内容を集約していくことで、改善につなげやすいルートができています。それ以外にも、製品を組み立てている製造グループ会社からの不具合もありますね…。
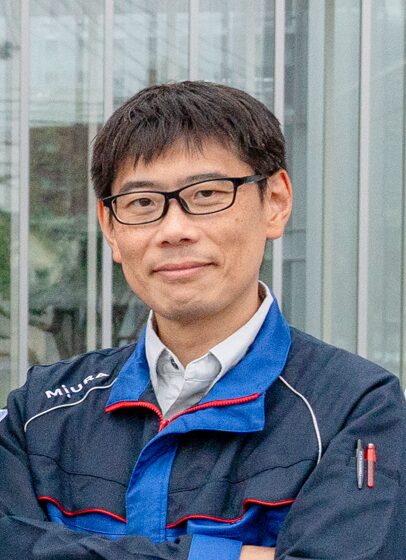
私は主に製造グループ会社からの不具合対応を担当しており、「組み立てがうまくいかない」という声を聞くことがあります。
ただ、今は3D CADを使っているので新商品の設計精度は向上し、今までのような「ネジが思った以上に入る・入らない」とか「部品と配管が干渉する」というような問い合わせは、減少傾向にあると思います。
他には、購入部品が製造中止になるなど、突然、部品が入手困難になる状況に陥ることがあります。「代替品がこれしかない…!」という時に、現状のレイアウトを使って「どうやって入れよう…。配管を変えたらスペース内に収まるかな?」とか、そういう検討を常々やっています。
製品の製造がストップして出荷ができなくなってしまうことがないよう、優先して対応していますね。
編集部:なるほど、結構フレキシブルな対応が求められるんですね。設計者へ直接要望がくるのは、製造グループ会社とメンテ技術部くらいでしょうか?
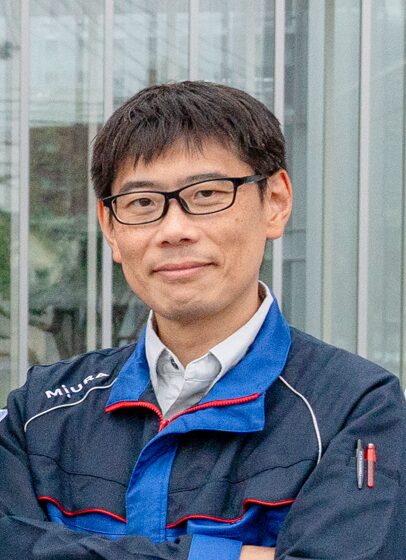
部品の供給管理を行う部門(パーツセンター)から相談がくることもあります。「マニュアルに載ってるんだけど、古い機種にこの部品、本当に使えますか?」みたいな問い合わせとか。自分の入社年より前に販売された古い機種の問い合わせもたまにくるので、昔の資料を引っ張り出してきたりして確認することもありますね。
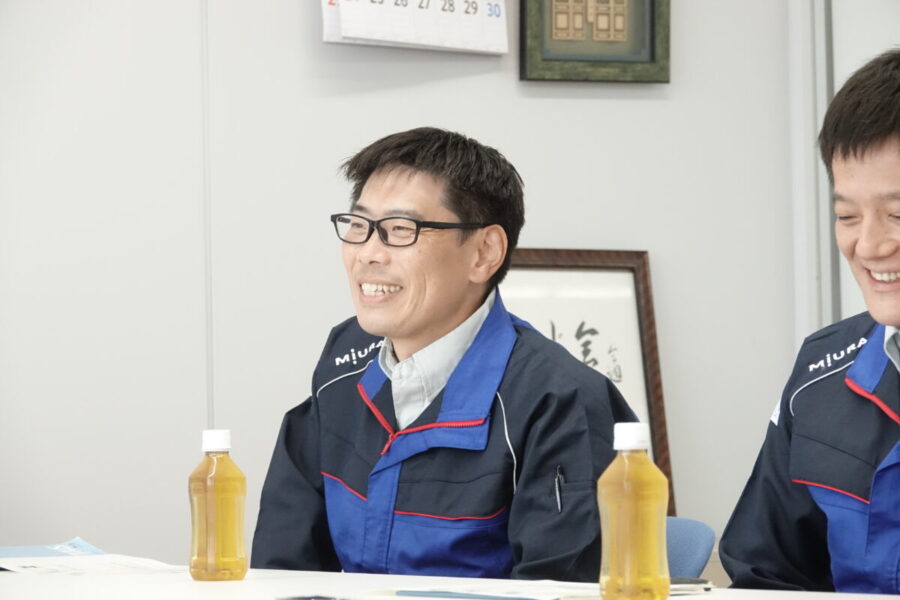
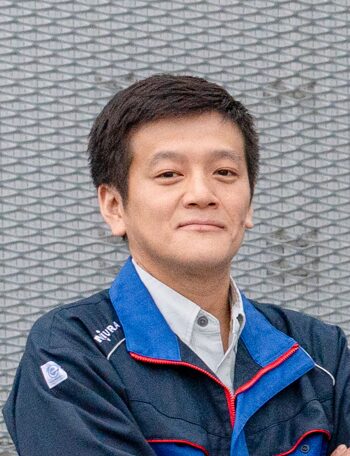
自分が生まれる前の機種の問い合わせが入ることもあって、驚いたこともあります。だいたいボイラの寿命って、10年~15年と言われているので。
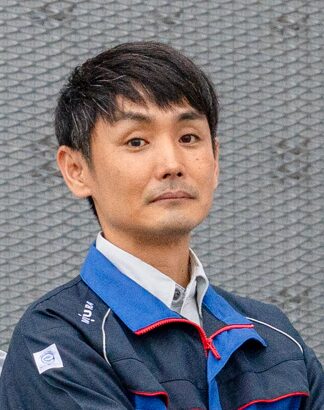
この前ありましたよね。「40年程前に販売したボイラに、この部品を使いたいんだけど、できますか?」ってお問い合わせが入った時は驚きました。運転頻度にもよるのでしょうけど、今も使い続けられていることに驚きです。ミウラのビフォアメンテナンス(※)のおかげかもしれませんね。
※オンライン上でお客様の機器を24時間見守りながら、定期点検にて先行で部品交換し、調整を行うことで故障やトラブルを未然に防ぐメンテナンス方法。
編集部: 他にも、設計者の仕事として、実験場に籠って実証実験などを行うこともあると聞いたのですが?
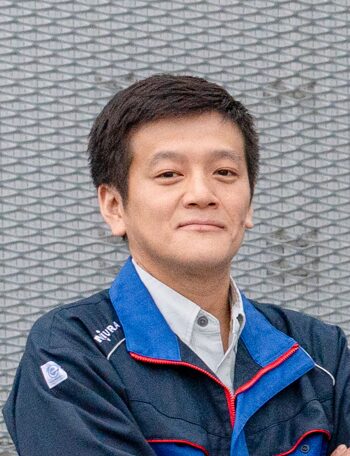
そうですね、どちらかというと若手社員に実証実験に張りついてもらうことが多いです。実験場での作業は地道ではありますが、成功した時の達成感はありましたね!今でも楽しかった思い出です。
納入先や取引先に足を運ぶ機会は?
編集部:技術部門の人たちが現場に製品を見に行く機会はあるのでしょうか?
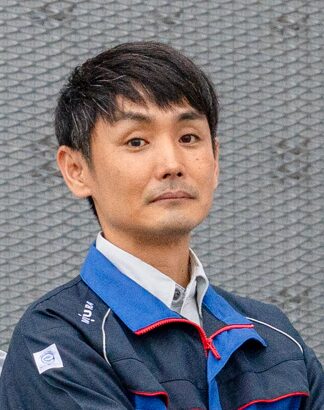
きっかけがないと、なかなか行けないですね…。
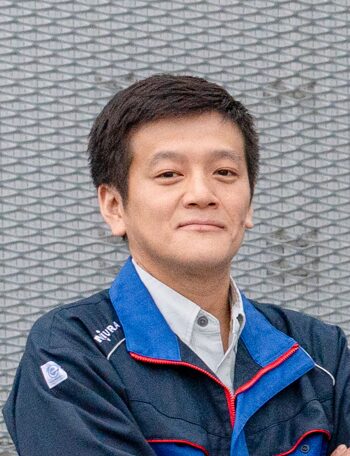
新商品を開発した時か、不具合が発生した時くらいでしょうか…。
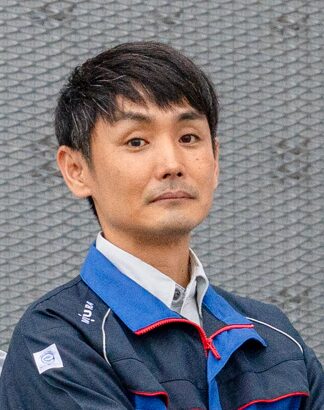
私が担当した新製品の初号機納入時は、現場(納入先)に行きました。何かあってはいけないので、納入直後はしばらく遠隔からも製品の状況をチェックするなどして、慎重に見届けました。
その時に大切にしたことは、現場のFEの方々へのヒアリングですね。FEの方々は、最前線でお客様と接していて、製品のお世話をしてくれているので、誰よりも状況をよく分かってくれているんですよね。
編集部:FEの方々は心強い存在なんですね!以前、ミウラplusの取材で、昔からお付き合いがあるサプライヤーの鉄工所さんとお話した時に「昔はもっと技術の人が現場(取引先)にも来ていた」という話があったんですが、実際どうですか?
彼らの技術力を知らずして、ミウラの製造は語れない!サプライヤー取材 vol.1 ~株式会社門田鉄工様~ | ミウラplus[ミウラプラス]
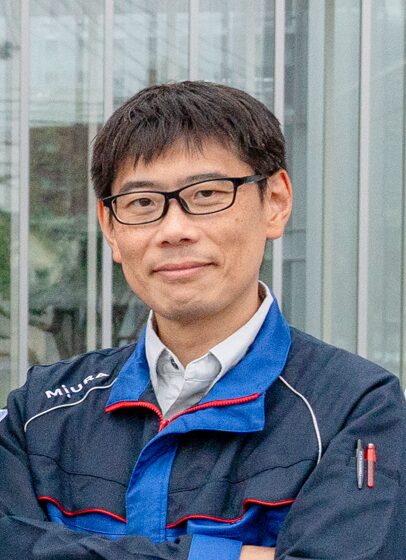
昔に比べると足を運ぶ機会は減ったのかもしれません。でも何かトラブルがあった時、何が起きているのか、実際のモノを見ないと分からないので、極力、現場に行って対応するようにしています。
「現場で現物を見て現実を知りなさい」と叩き込まれているので。
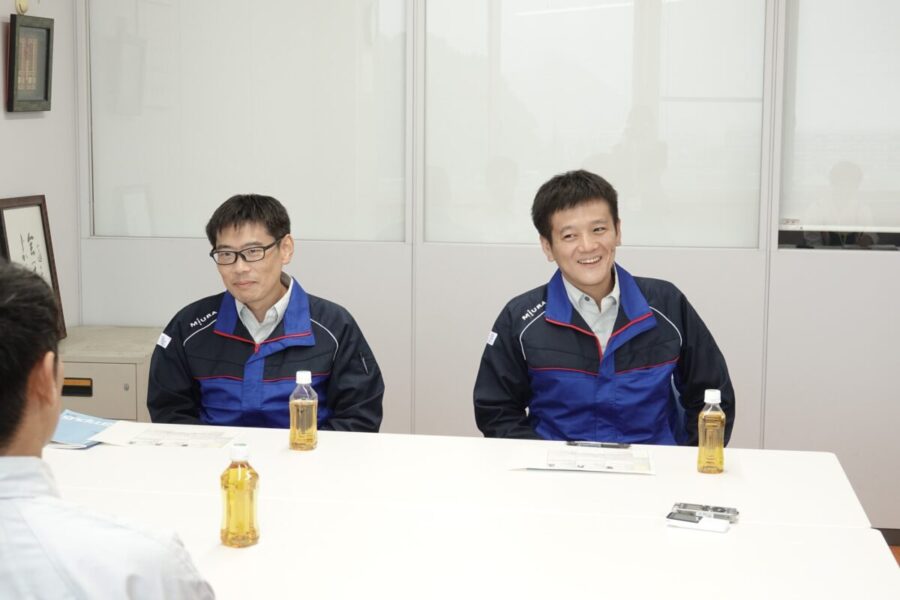
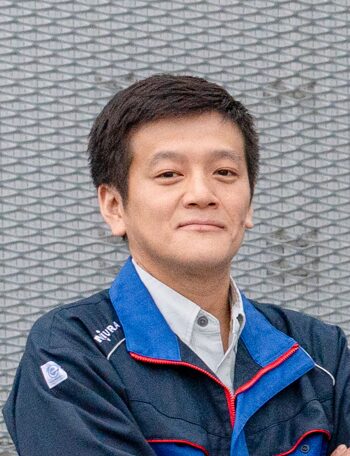
「会ってじかに話せ」と創業者・三浦保さんの今週の言葉にもありましたよね。ほら!たまたまこの会議室にも掲示されています。
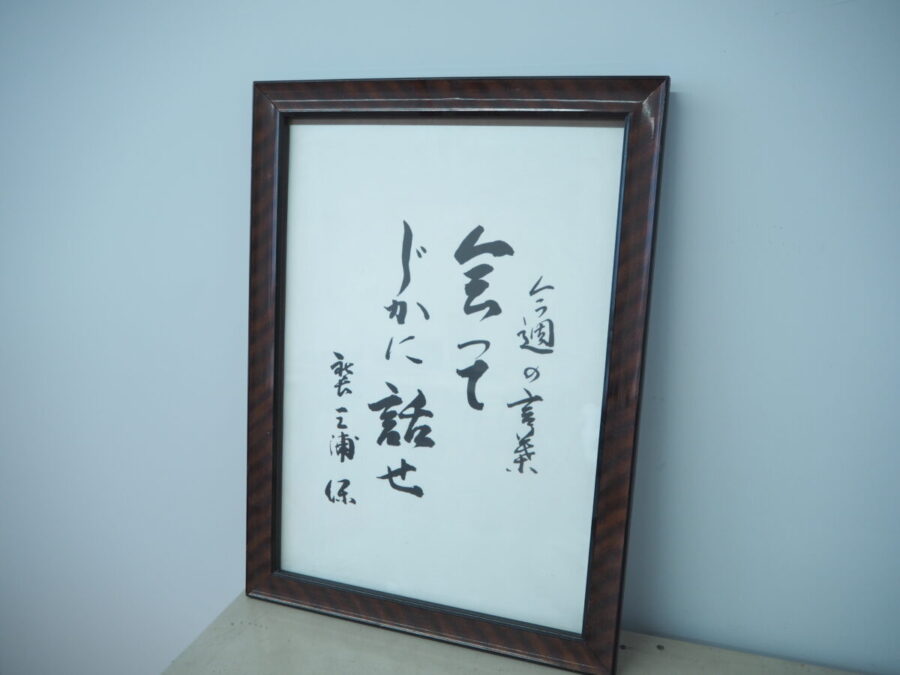
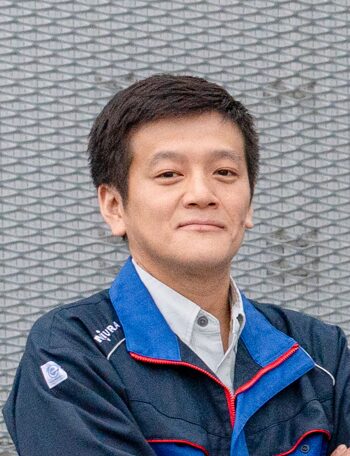
IT技術が発達して直接会う機会も減ってきていますが、やっぱり、メールや電話だけでなく、人と直接会って話すと気持ちもより伝わりますよね。
編集部: そうですよね。改めて創業者のこの言葉を大切に、意識的に行動に移したいですよね。
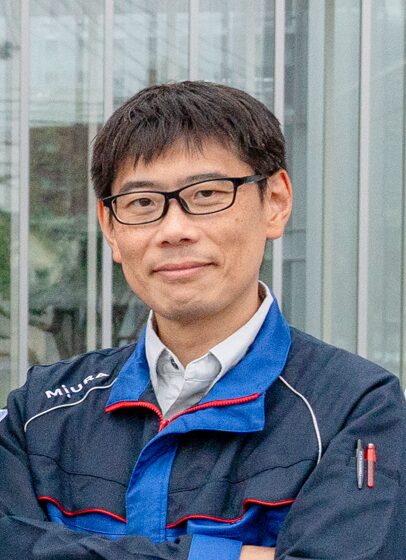
あと、昔は少しのミスでも、厳しく指摘されることがあったそうですが、今はそうしたことも減っています。いいものづくりを行うには、厳しいご意見も大切に対応していきたいですね。
設計者の業務で一番大切にしていることは?
編集部:設計者の業務で一番大切にしてることってありますか?
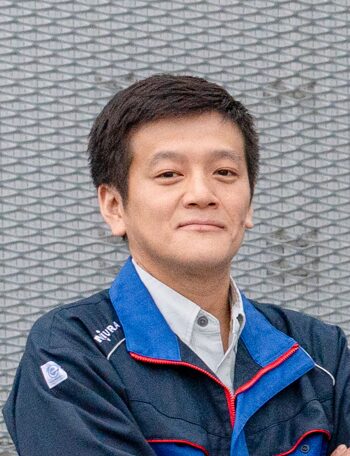
やはり一番は「安全」ですね。製品はお客様が使用されるものなので、お客様が怪我をしない作りになっていることも大事だと思います。
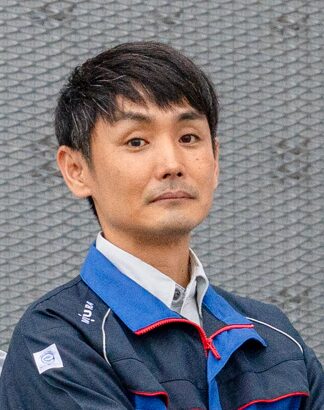
新人の頃は、どちらかといえば性能・品質重視で、何よりも「異常(アラーム)が出ないこと」を意識していた気がします。正直、その頃は現場のことをほとんど知らなかったので。
でも、FEの経験を通じて、FEからの要望も自分事のように理解できるようになり、メンテナンスのしやすさ・使いやすさも大事だと考えるようになりました。
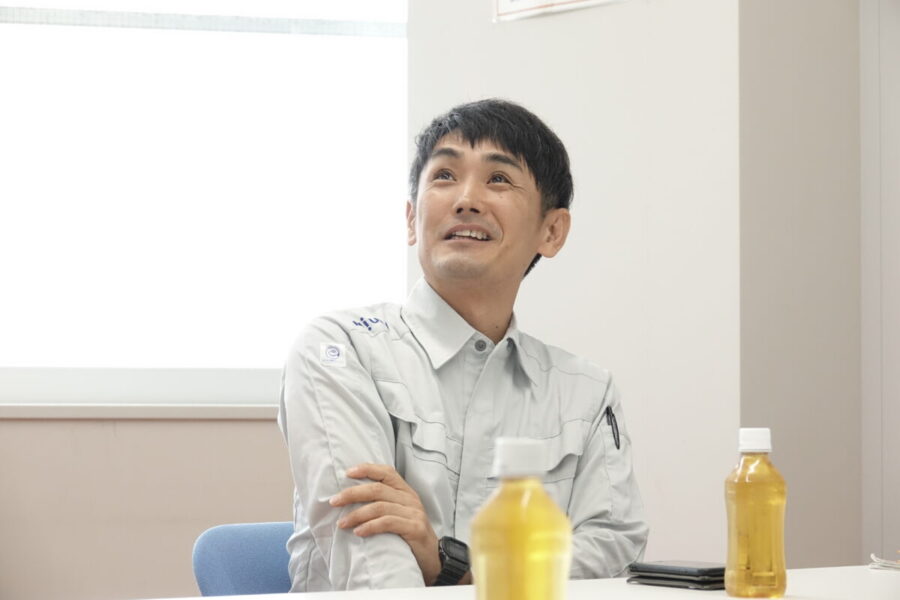
コストダウンについて
編集部:「コストダウンを求められるけれど、追求しすぎると品質が落ちてしまい、逆にお金と時間がかかる」ということを耳にしたのですが、いかがでしょうか。
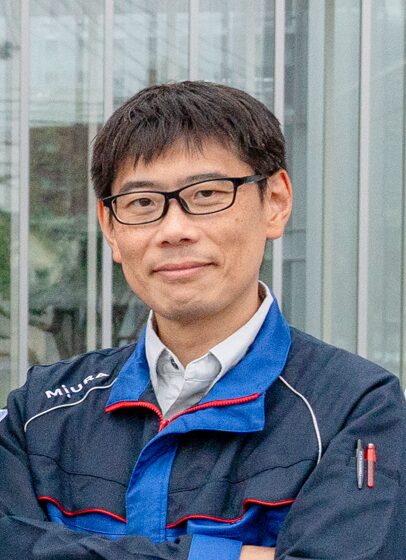
過去にあったものとしては、調達関連の部門から「海外製の安価な部品を採用してくれませんか?」との提案が来ること。もちろん品質や耐久性なども確認した上で採用したものの、使っていくうちに不備が出てきたとか、海外での管理費用がすごくかかっていたとかで、結局国内製造のものに戻したということはありましたね。
編集部:メンテナンス作業をしているFEさんたちは、作業している中で「この部品が良くないのかも…?」と気づくこともあるのでしょうか?
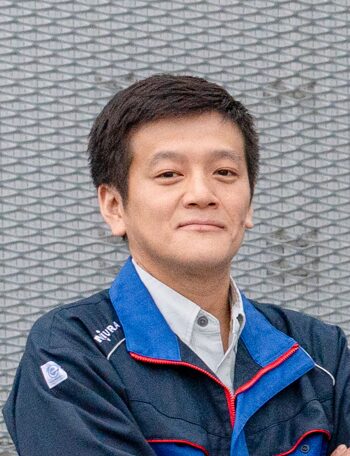
あると思います。短期間で同案件が続くと、我々技術部側でも「あれ?もしかして…」ってなりますよね。
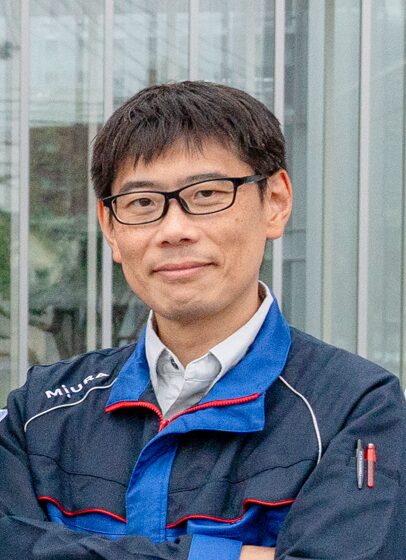
一時期、部品の樹脂化に力を入れていた時期があり、材料を樹脂に変更してトライ&エラーを繰り返しながら基準をクリアし、製品に搭載した部品がありました。しかしながら、実際のボイラの設置環境では想定以上の温度となっているケースもあり、使用している間に変形し不具合の原因になってしまったという事例がありました。
コストダウンのはずが結果的にコストもかかり、多くの方にご迷惑をお掛けすることになってしまいました。
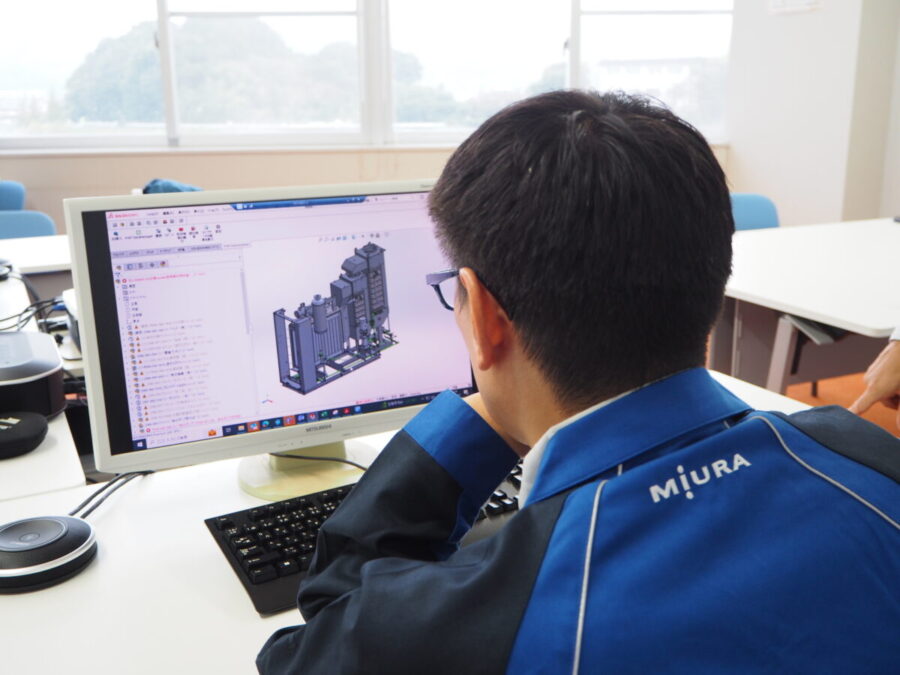
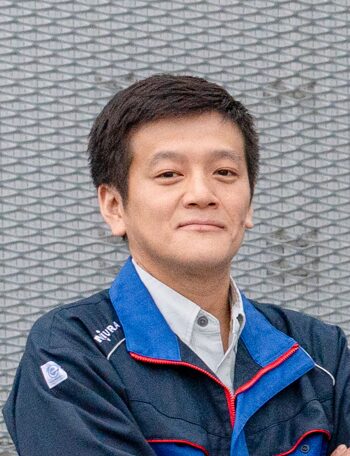
コストダウンについては、昔からずっと意識していますが「品質に勝るコストダウンはない」という言葉もありますよね。結局、部品を数十万円コストダウンできても、一発不具合が発生してしまうと元も子もないので。コストダウンよりも「まずは品質第一で」というところは、昔から念頭にあります。
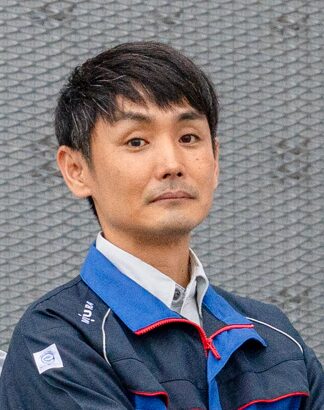
当然、標準ボイラ量産部隊としては、コスト意識は持つようにしていますが、やはり品質優先ですよね。
改善には時間がかかる!?
編集部:FEの方々から、「ここを改善してほしい」という要望を受け入れてもらうのにすごく時間がかかるというのを聞いたのですが、設計者から言わせると、要望を受け入れるまでにはたくさんの工程があるんですよね?
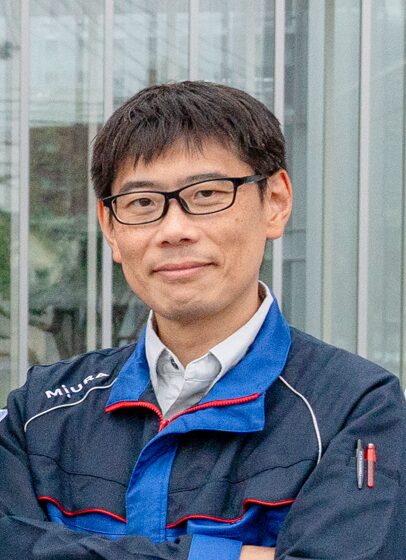
そうですね。例えば、AからBの部品に変えて欲しいという要望が上がってきたとします。
まず、その部品が採用できるかどうかを判断し、採用できる場合は、製品への反映・レイアウト検討を行います。
改変指示票という帳票を設計者が作成して確認項目を洗い出し、改変検討会にて設計者から上位役職者へ詳細説明を行い、その場で承認を得る。
その後、実験場で検証を重ねてデータをまとめたり、部品表変更・図面作成など…やることはたくさんあります。
また、設計側の部品表だけでなく、製造側の部品表の変更も必要なので、1つの部品を変更するだけでもトータルで数ヶ月必要になってきます。
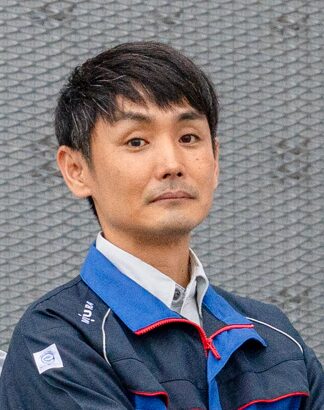
現場のみなさんがどういうイメージを持っているか分からないですけど、多分思っているよりも、かなりのステップがあると思います。
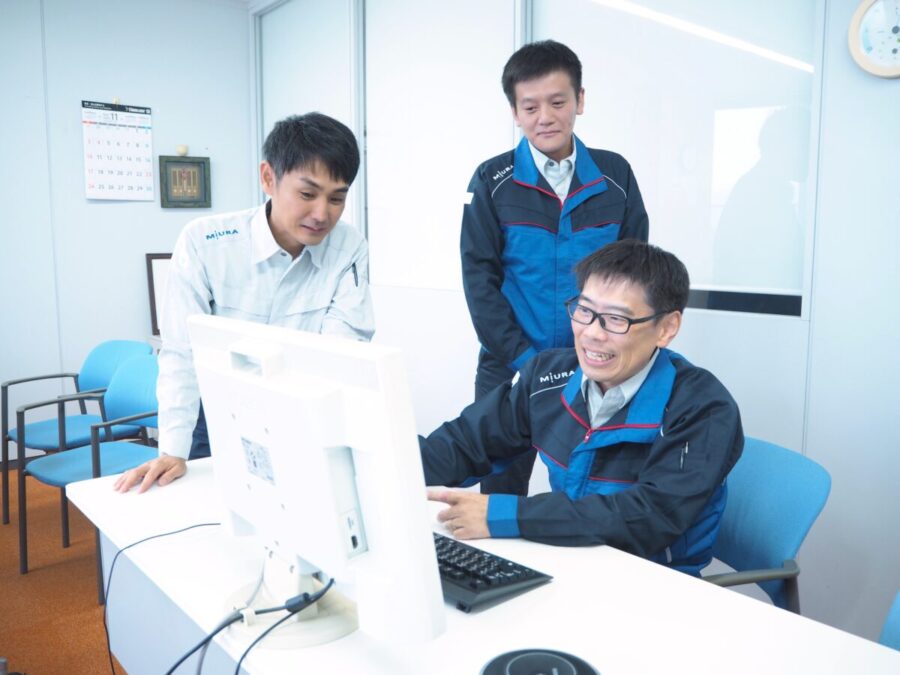
まとめ
前回の、FEさんの問いかけ・疑問に対する答えがしっかり返ってきた2回目の取材。設計者としての言い分、思いが伝わってきました。次回は、いよいよFEと設計者が直接対談!どんなトークが繰り広げられるか楽しみです。
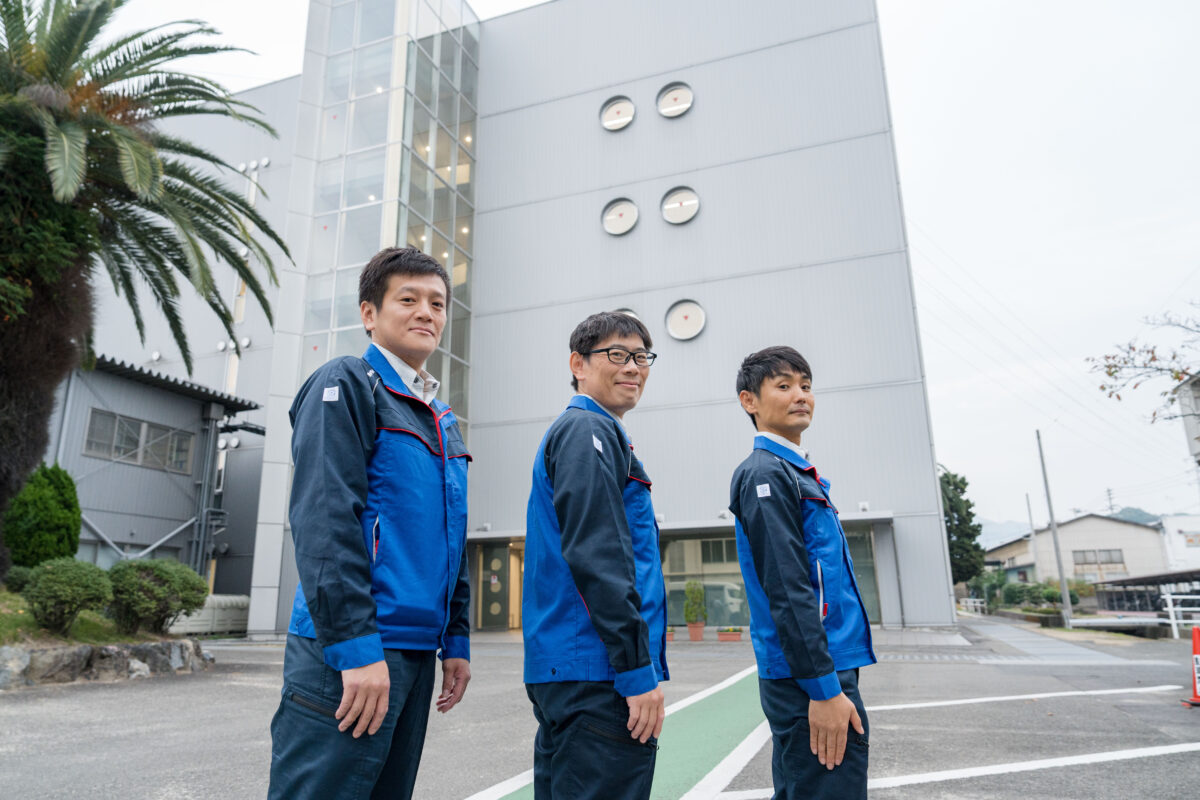